China dominates global Polycarboxylate Superplasticizer (PCE) production, accounting for 60% of worldwide output. This article explores how leading manufacturers optimize supply chains, ensure quality, and innovate to meet rising demand for high-performance concrete solutions.
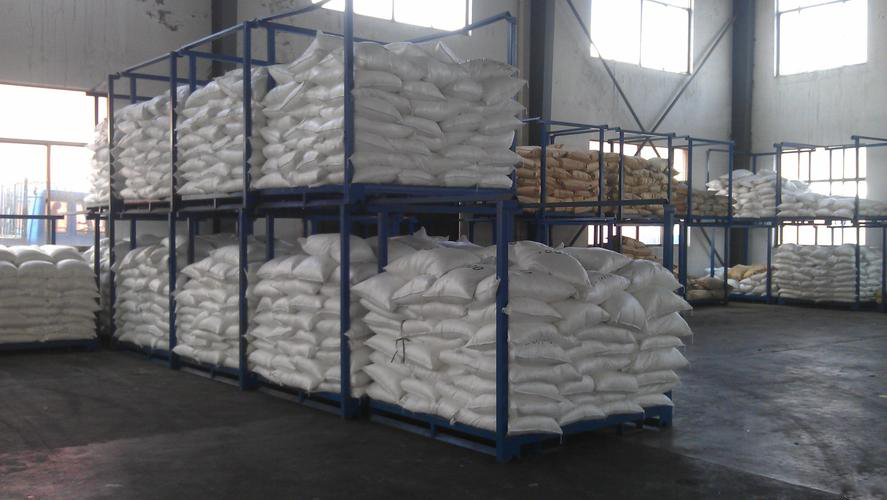
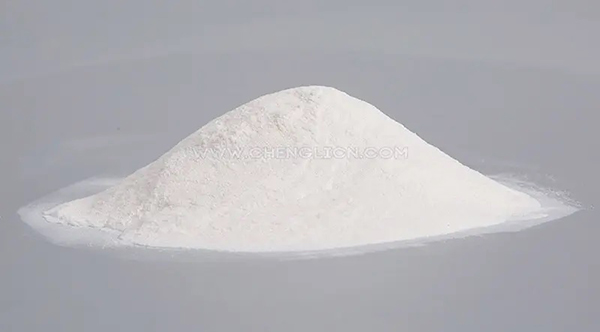
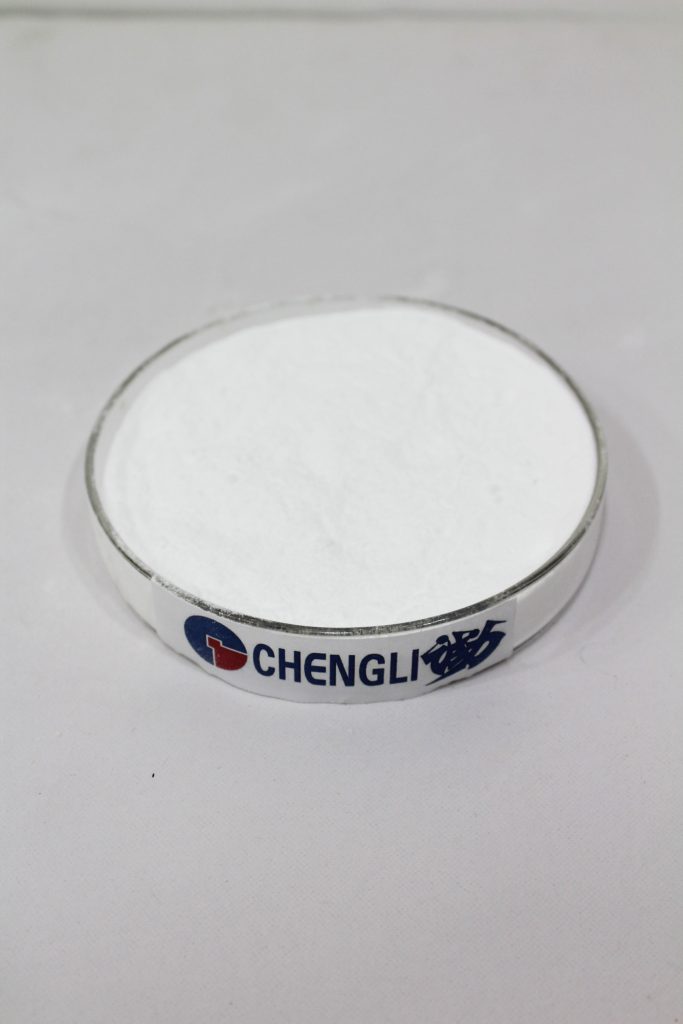
1. Raw Material Sourcing Strategies
Chinese producers prioritize local raw materials to reduce costs and logistics risks. Key components include:
- Monomers: Synthesized from ethylene oxide (EO) and acrylic acid, sourced from domestic petrochemical giants like Sinopec.
- Water Reducing Agents: Blended with locally produced polycarboxylate polymers for tailored performance.
- Additives: Fly ash and slag from steel mills are integrated to enhance sustainability.
Best Practice: Vertical integration allows manufacturers like Sany Heavy Industry to control monomer production, ensuring consistent quality and cost efficiency.
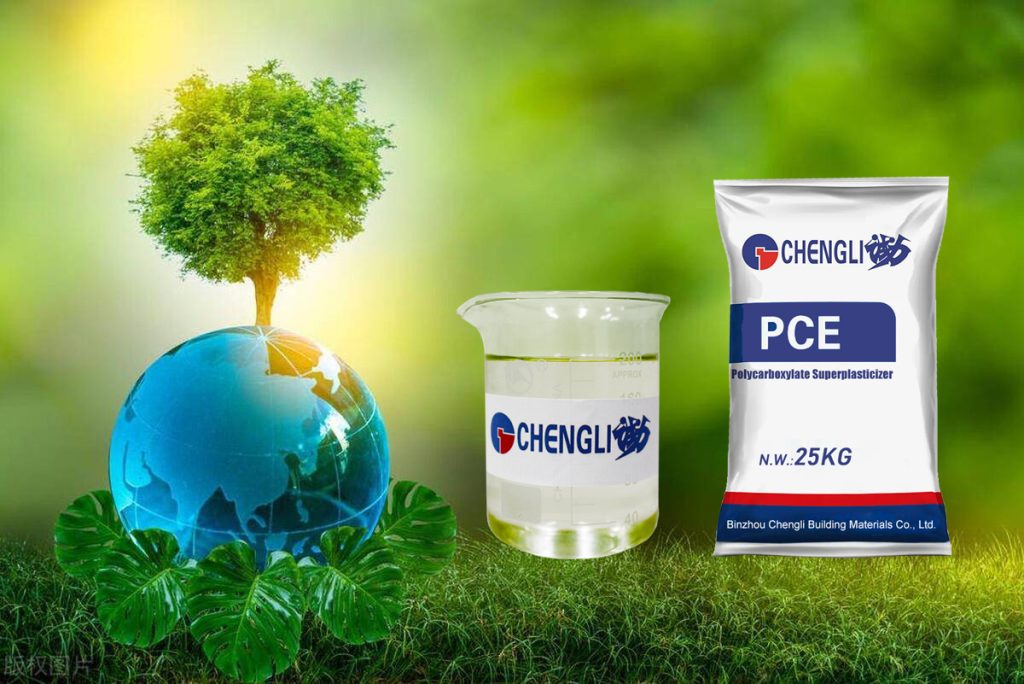

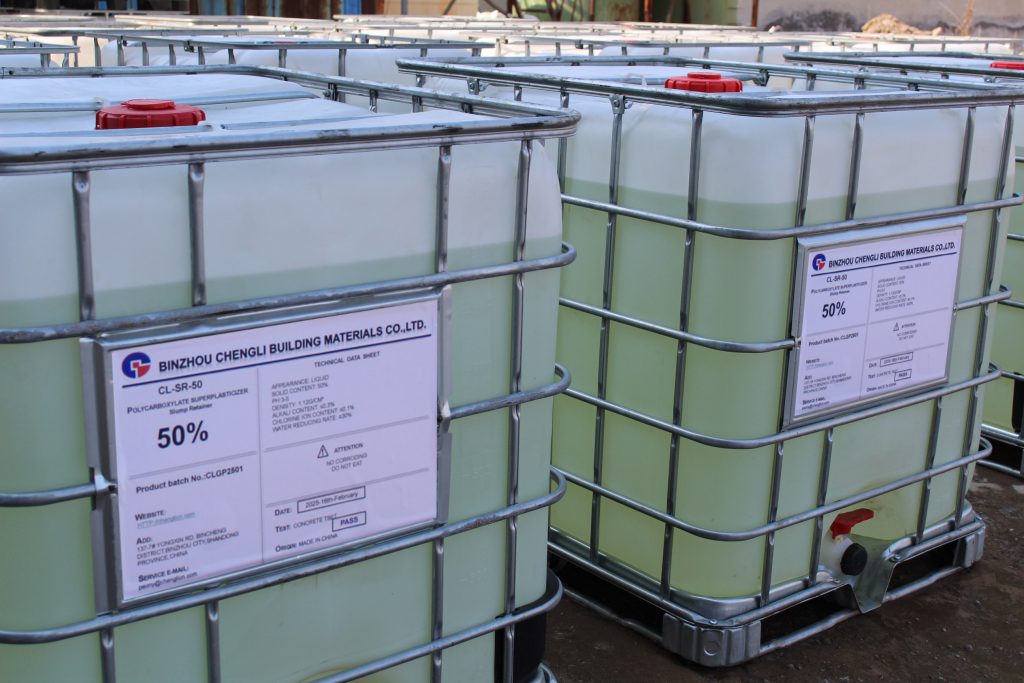
2. Production Process Optimization
Advanced manufacturing techniques drive China’s PCE leadership:
- Batch Reactors: Automated systems precisely control polymerization temperatures (±2°C) for uniform molecular weight distribution.
- Modular Facilities: Plants in Shandong and Jiangsu provinces scale production to 500,000+ tons annually while maintaining flexibility.
- Waste Management: Closed-loop systems recycle 95% of wastewater, aligning with green manufacturing goals.
Innovation Spotlight: Leading firms use AI-driven algorithms to predict optimal mix ratios, cutting R&D time by 30%.
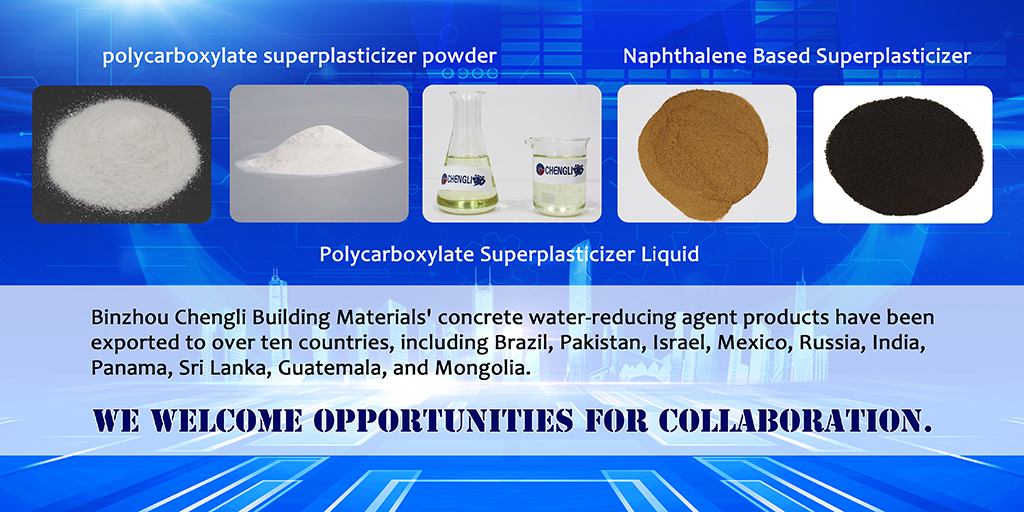
3. Quality Control Standards
Stringent protocols ensure PCE meets global specifications:
- Laboratory Testing: All batches undergo slump retention, water reduction rate, and chloride ion tests.
- ISO 9001 Compliance: Producers like China National Building Material Group maintain certification across facilities.
- Real-World Validation: Products are field-tested in major projects, such as the 2025 Guangdong-Hong Kong-Macao Bay Bridge expansion.
Key Insight: Chinese PCE consistently achieves 35-40% water reduction, surpassing ASTM C494 Type G requirements.
4. Sustainability-Driven Practices
Environmental responsibility shapes production:
- Low-Carbon Formulations: 20% of PCE output now includes bio-based monomers derived from corn starch.
- Energy Efficiency: Solar-powered reactors in Xinjiang reduce carbon intensity by 45%.
- Circular Economy: Recycled concrete aggregates are blended into 30% of production batches.
Government Support: Subsidies under China’s 14th Five-Year Plan incentivize green PCE innovation.
5. Global Market Expansion
Chinese manufacturers are increasingly exporting advanced PCE:
- Key Markets: Europe (25% of exports), Southeast Asia (30%), and North America (18%).
- Customization: Products are adapted for regional needs, such as cold-weather formulations for Russia.
- Partnerships: Joint ventures with global firms like BASF enhance technology transfer and distribution networks.
Growth Projection: China’s PCE exports are expected to reach $1.2B by 2030, driven by infrastructure projects under the Belt and Road Initiative.
Conclusion
China’s PCE production combines technical excellence, supply chain resilience, and sustainability to lead global markets. By adopting best practices in raw material sourcing, process automation, and green innovation, manufacturers continue to set industry standards.
Contact Leading Chinese PCE Producers to explore collaboration opportunities for your next construction project.