In the dynamic world of construction, manufacturing, and infrastructure development, the demand for specialized materials continues to grow. Projects vary in scope, environment, and objectives, requiring solutions that go beyond one-size-fits-all approaches. Customized admixtures have emerged as a critical tool, enabling engineers and developers to meet unique challenges with precision. This article explores how these tailored solutions address specific project needs, enhance performance, and drive innovation across industries.
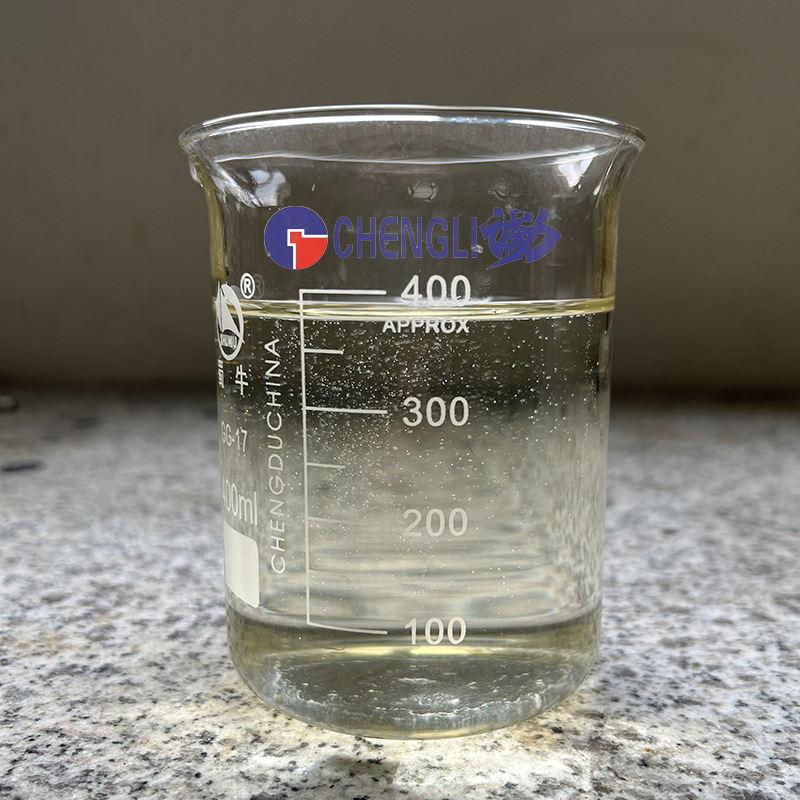
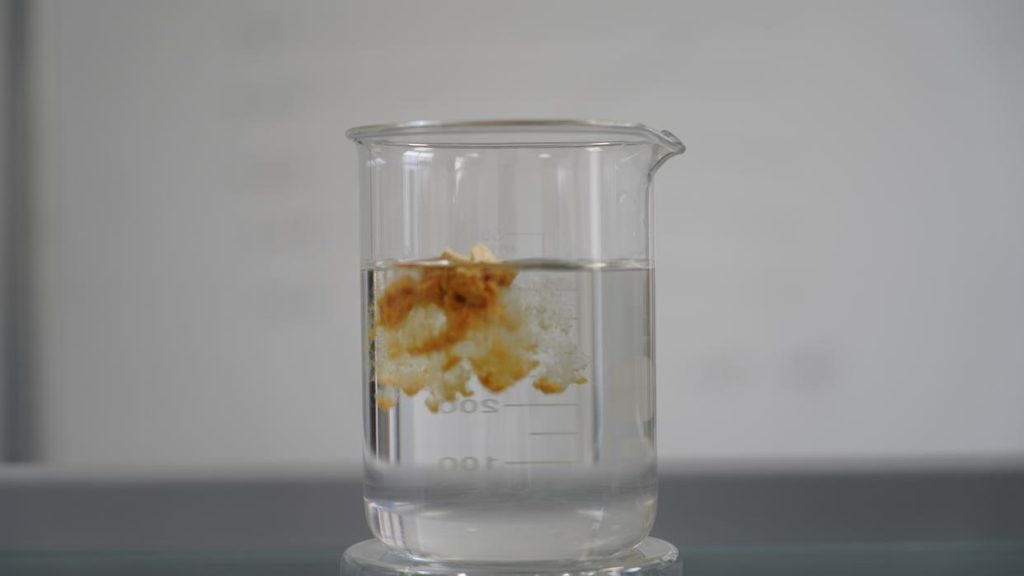
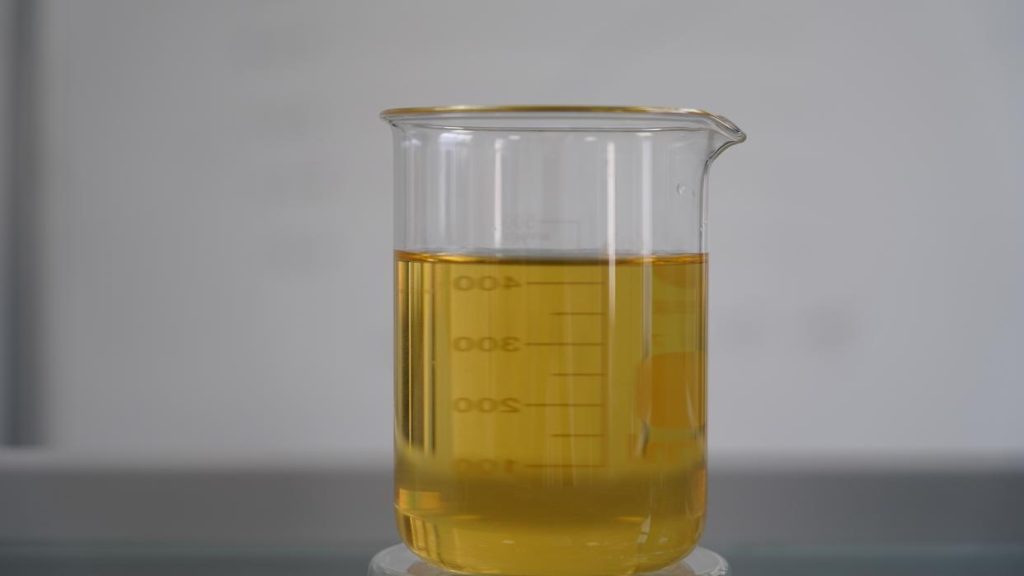
1. The Basics of Admixtures: Why Customization Matters
Admixtures are substances added to construction materials like concrete, mortar, or asphalt to modify their properties. They can improve strength, durability, workability, or curing time. While standard admixtures serve general purposes, many projects require more. Extreme weather conditions, complex structural designs, or strict regulatory standards often demand bespoke solutions.
Customization allows engineers to adjust admixture formulations. They can target specific performance metrics, such as resistance to chloride ingress, reduced shrinkage, or enhanced thermal conductivity. By analyzing project requirements, manufacturers create admixtures that integrate seamlessly with local materials and environmental factors. This proactive approach eliminates guesswork, ensuring optimal results from the first mix.
2. Key Industries Benefiting from Tailored Admixtures
2.1. Construction and Infrastructure
In large-scale construction, every project has unique variables. A high-rise building in a coastal city needs concrete that withstands saltwater corrosion. A bridge in a freeze-thaw zone requires admixtures to prevent cracking from repeated temperature changes. Customized solutions address these needs by enhancing material resilience.
Engineers collaborate with admixture experts to identify challenges. They consider factors like aggregate type, cement composition, and curing conditions. For example, a dam project might need admixtures to reduce heat of hydration, preventing thermal cracking in massive concrete pours. Such tailored formulations ensure structures meet safety standards and last longer.
2.2. Manufacturing and Industrial Applications
Manufacturers of precast concrete products, asphalt, and composite materials also benefit from customization. Precast plants producing intricate architectural elements need admixtures that improve mold release and surface finish. Industrial floors exposed to heavy machinery require solutions that enhance abrasion resistance and load-bearing capacity.
Customized admixtures can also optimize production processes. Faster setting times can reduce downtime in precast manufacturing, while improved flowability allows for complex designs without compromising strength. By aligning admixture properties with manufacturing goals, companies boost efficiency and product quality.
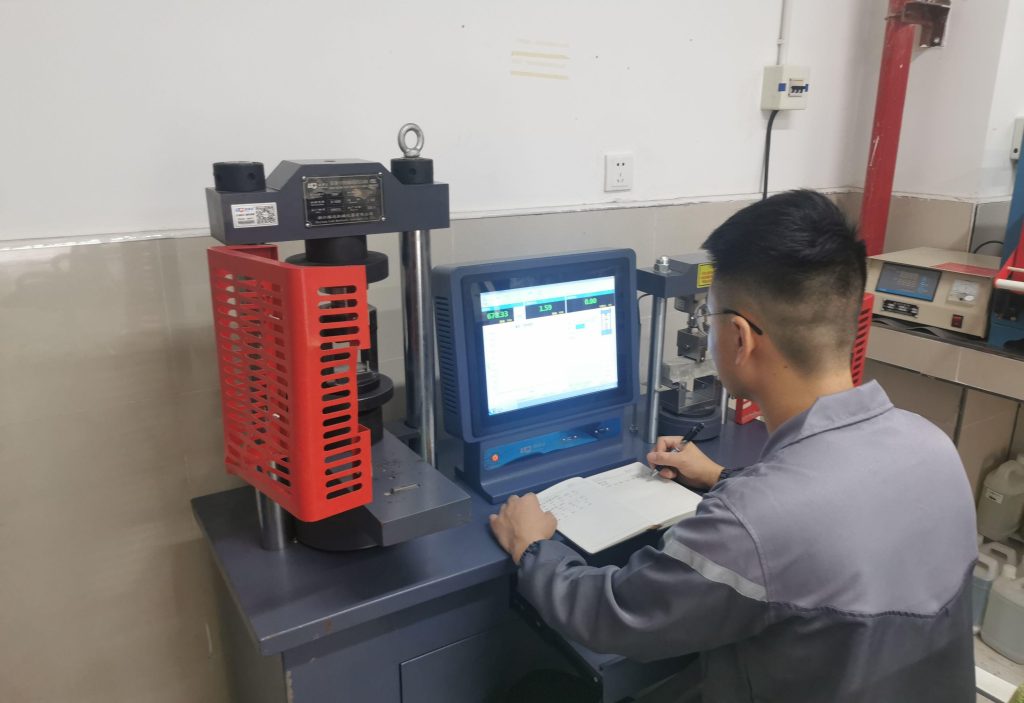
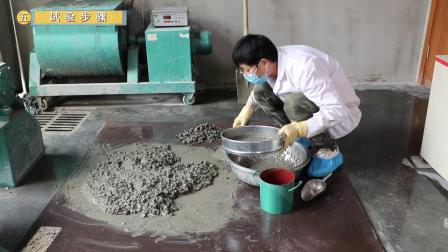
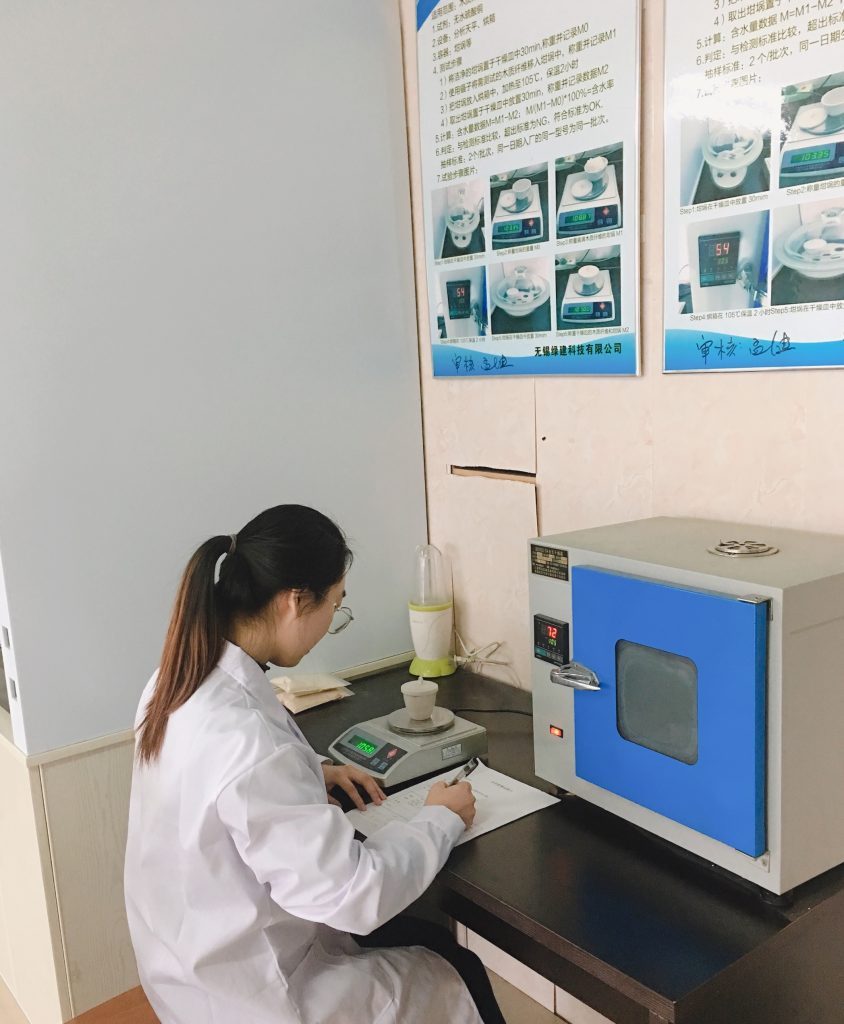
2.3. Renovation and Repair Projects
Renovation work presents unique challenges, such as bonding new materials to old structures or restoring historic buildings. Customized admixtures can improve the compatibility between new and existing materials, ensuring strong bonds and long-term durability. For concrete repair, solutions that match the shrinkage properties of the original structure prevent new cracks from forming.
In heritage preservation, admixtures must meet strict conservation standards. They need to be non-disruptive to historic materials while providing necessary reinforcement. Tailored formulations allow engineers to balance performance with preservation, ensuring renovations are both effective and respectful of architectural history.
3. The Customization Process: From Analysis to Application
3.1. Project Assessment and Data Collection
The first step is understanding the project’s requirements. Engineers gather data on material specifications, environmental conditions, and performance goals. They consider factors like temperature, humidity, exposure to chemicals, and expected load conditions. This detailed analysis forms the basis for creating a targeted admixture formula.
3.2. Formulation Design and Testing
Using the project data, admixture manufacturers design preliminary formulations. They select from a range of chemical components, such as superplasticizers, accelerators, or corrosion inhibitors, adjusting concentrations to meet specific needs. Laboratory testing follows, evaluating properties like compressive strength, setting time, and resistance to environmental factors.
Testing is rigorous and iterative. Samples are subjected to simulated real-world conditions, ensuring the admixture performs as intended. For example, a formulation designed for high-temperature environments might be tested under prolonged heat to measure stability and durability.
3.3. Collaboration and Iteration
Successful customization requires collaboration between all stakeholders—engineers, contractors, and manufacturers. Feedback from the field helps refine formulations. If a contractor notices issues with mixability on-site, the admixture can be adjusted to improve workability without compromising other properties. This iterative process ensures the final solution is practical and effective.
3.4. Scaling and Implementation
Once a formulation is validated, it moves to production. Manufacturers ensure consistent quality control, using advanced mixing and testing technologies. They also provide technical support during implementation, guiding contractors on proper admixture dosage and mixing procedures. This support minimizes errors and maximizes the admixture’s benefits.
4. Advantages of Customized Admixtures Over Standard Solutions
4.1. Enhanced Performance
Standard admixtures offer general benefits, but customized solutions deliver targeted performance. For example, a concrete mix designed for a tunnel project might need both high early strength for fast construction and low permeability to prevent water ingress. A tailored admixture can achieve both goals simultaneously, whereas standard products might require compromises.
4.2. Cost Efficiency
While customized admixtures may have higher upfront costs, they often save money in the long run. By addressing specific issues like material waste, rework, or premature degradation, they reduce lifecycle costs. A structure built with durable, tailored materials requires fewer repairs and has a longer service life, providing a better return on investment.
4.3. Environmental Sustainability
Customization also supports green building initiatives. Admixtures can be designed to reduce material consumption—for example, by improving concrete strength to allow thinner structural sections. They can also enhance recyclability or use eco-friendly components, aligning with global efforts to minimize construction’s environmental impact.
4.4. Flexibility in Design
Modern architecture and engineering demand innovative designs, from curved concrete facades to lightweight composite materials. Customized admixtures enable these designs by enhancing material workability and performance. They allow engineers to push creative and structural boundaries without sacrificing safety or durability.
5. Case Studies: Real-World Impact of Tailored Admixtures
5.1. Coastal High-Rise in Miami, USA
A luxury high-rise project in Miami faced challenges from saltwater exposure and high humidity. Standard admixtures could not fully protect the concrete from chloride-induced corrosion. A customized solution was developed, incorporating corrosion inhibitors and hydrophobic agents. The admixture improved the concrete’s density, reducing water absorption and extending the structure’s lifespan by over 20%.
5.2. High-Speed Railway in China
China’s extensive high-speed railway network requires tracks that can withstand heavy loads and rapid temperature changes. Customized admixtures were used to create concrete with high early strength for fast track laying and low shrinkage to maintain alignment precision. The solutions reduced construction time by 15% while meeting strict safety standards.
5.3. Historic Bridge Restoration in Rome, Italy
The restoration of a historic Roman bridge needed admixtures that would bond new mortar to ancient stone without damaging the original structure. A bespoke formulation was developed using natural pozzolans and low-alkali components, ensuring compatibility and preserving the bridge’s historical integrity while providing necessary reinforcement.
6. Challenges and Considerations in Admixture Customization
While the benefits are clear, customization requires expertise and resources. Not all projects justify the investment in bespoke solutions, especially smaller ones with standard requirements. Engineers must weigh the project’s complexity, budget, and long-term goals to decide if customization is necessary.
Another challenge is ensuring consistency in raw materials. Admixture performance can be affected by variations in local aggregates or cement types, requiring ongoing testing and adjustments. Collaboration between manufacturers and contractors is crucial to address these variables and maintain quality.
7. The Future of Customized Admixtures: Innovation and Technology
Advances in materials science and data analytics are transforming admixture customization. Machine learning algorithms can analyze vast datasets of material properties and project conditions to predict optimal formulations faster. 3D printing and nanotechnology also offer new possibilities, enabling admixtures that self-heal cracks or adapt to changing environments.
Sustainability will remain a key focus, with more emphasis on bio-based components and circular economy principles. Admixtures that enhance the reuse of construction waste or reduce carbon footprints will become increasingly important as global environmental standards tighten.
Conclusión
Customized admixtures are more than just additives—they are strategic solutions that empower projects to overcome unique challenges. By tailoring formulations to specific needs, industries can achieve higher performance, durability, and efficiency while embracing innovation and sustainability. As projects grow more complex and demanding, the role of customized admixtures will only become more critical. Engineers and manufacturers who prioritize collaboration, data-driven design, and continuous improvement will lead the way in delivering solutions that shape the future of construction and manufacturing.
Whether building a skyscraper, restoring a historic landmark, or developing advanced industrial materials, the right admixture—customized for the task—can make all the difference. It’s not just about meeting standards; it’s about exceeding expectations, one tailored solution at a time.