Development Status of Concrete Water Reducer
The development water reducing admixtures has gone through three stages:the first generation general water reducing admixture stage represented by wood calcium, the second-generation high efficiency water reducer mainly represented by naphthalene series (mainly naphthalene sulfonate series, sulfonated melamine series, aliphatic series, sulfamate series etc.) stage and the third-generation high performance water reducing admixture stage represented by Πολυκαρβοξυλικός υπερρευστοποιητής. The market share of Πολυκαρβοξυλικός υπερρευστοποιητής is increasing year by year.
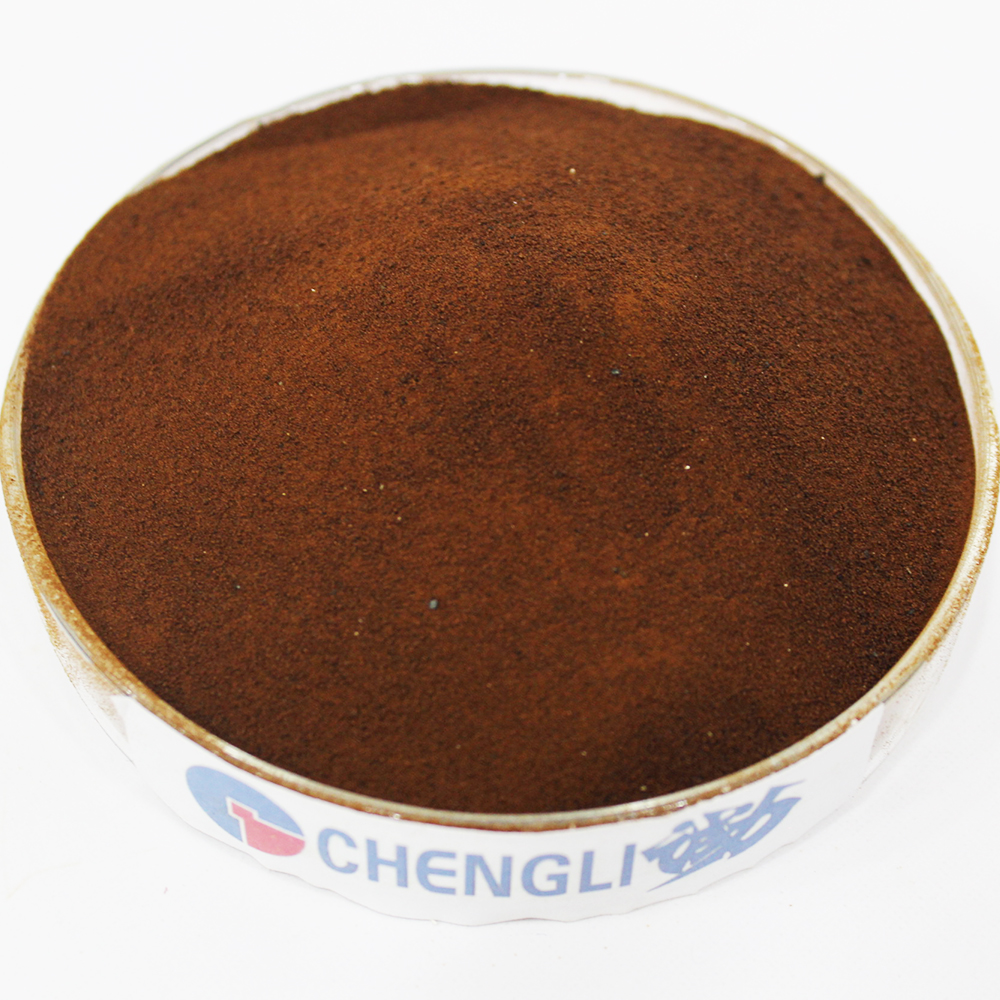
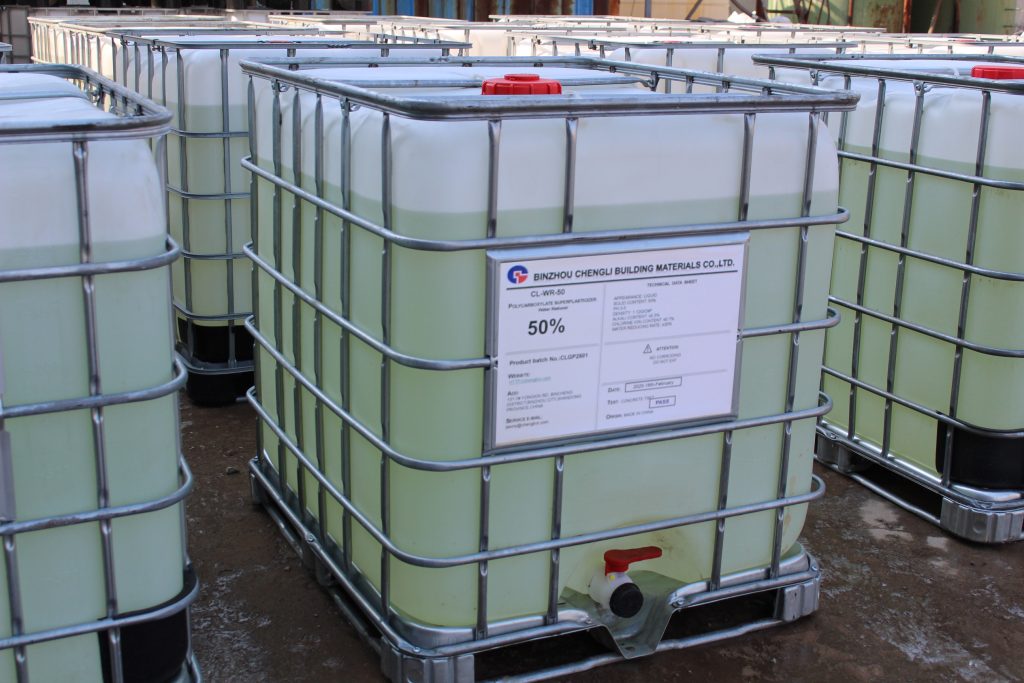
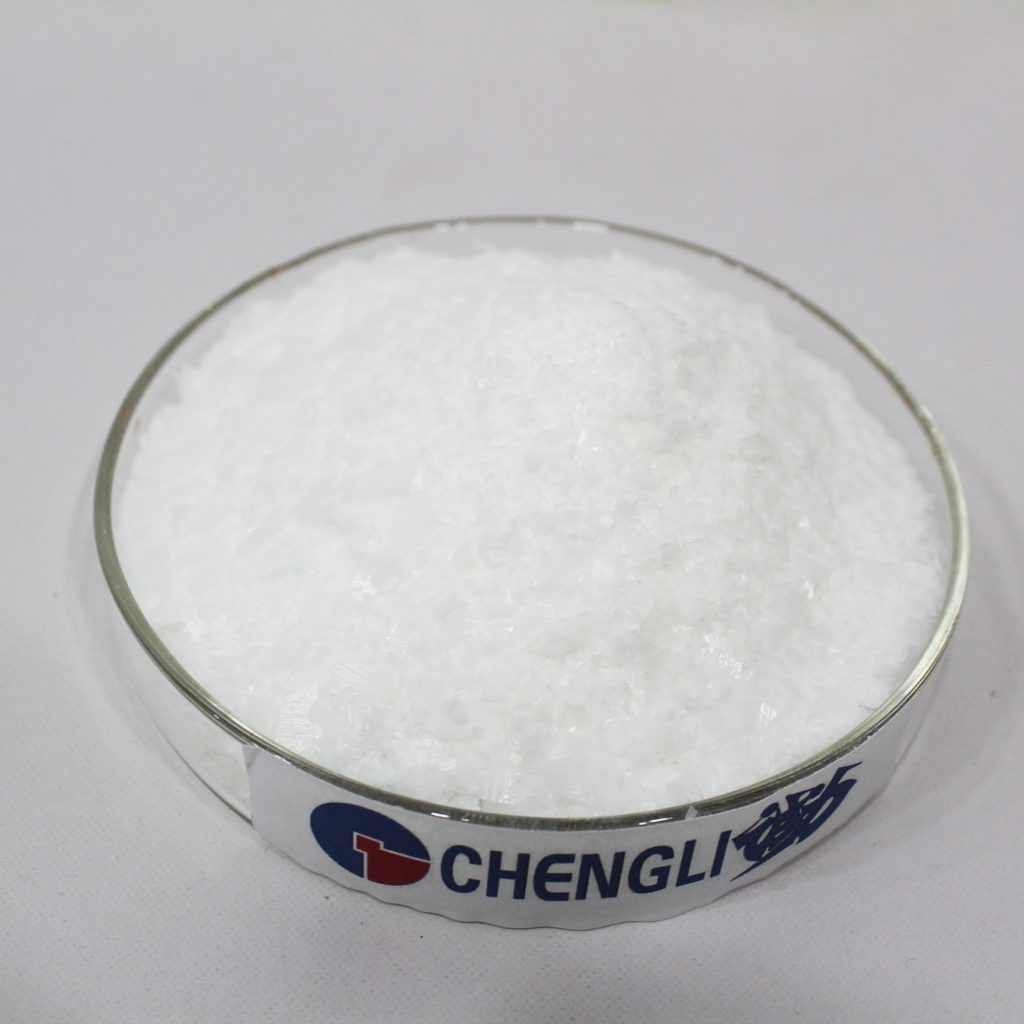
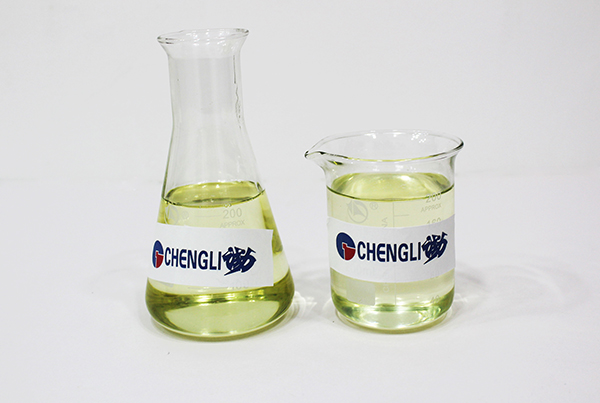
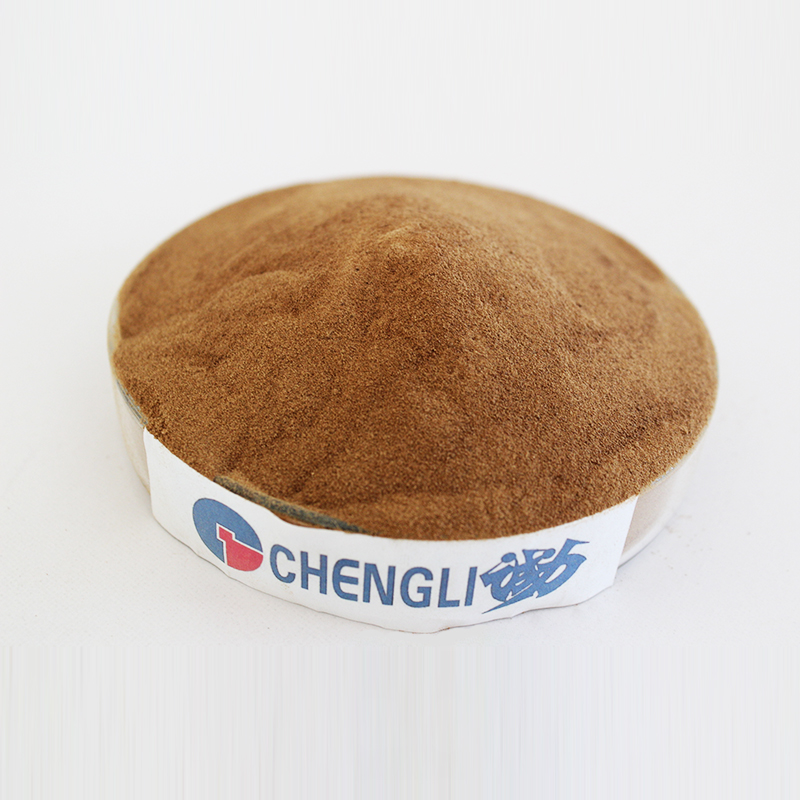
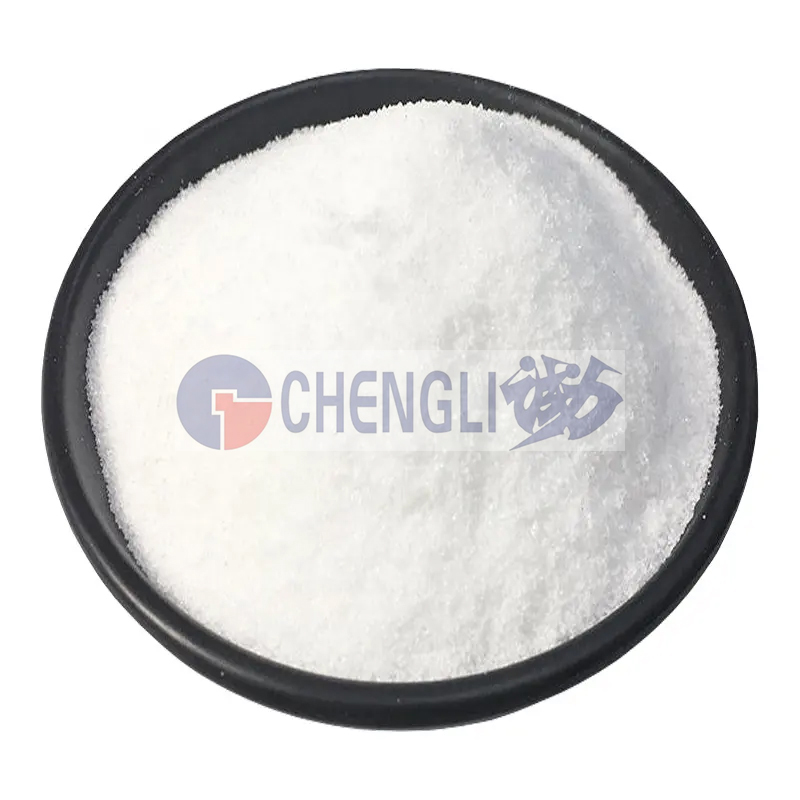
Polycarboxylate Superplasticizer Introduction
Polycarboxylate superplasticizers are widely used in modern concrete production due to their ability to enhance workability, reduce water content, and improve strength.However, improper use or compatibility issues can lead to challenges such as excessive slump loss, delayed setting, or reduced durability. This article explores common problems encountered with Polycarboxylate superplasticizers, their underlying causes, and actionable solutions to optimize concrete performance. By following these guidelines, construction professionals can ensure consistent, high quality concrete mixes while minimizing costs and delays.
1. Compatibility Issues Between Polycarboxylate superplasticizers and Cement
One of the most frequent problems with Polycarboxylate superplasticizers is poor compatibility with cementitious materials. This can manifest as rapid slump loss, insufficient dispersion, or even flash setting.
Causes:
- Cement composition: High tricalcium aluminate (C₃A) content or sulfate levels in cement can react unpredictably with Polycarboxylate superplasticizers.
- Admixture dosage: Overdosing or underdosing Polycarboxylate superplasticizers may disrupt the water-cement ratio and dispersion efficiency.
- Water quality: Impurities in mixing water (e.g., high chloride or sulfate content) can interfere with Polycarboxylate superplasticizers performance.
Solutions:
- Conduct compatibility tests: Use slump retention tests to evaluate Polycarboxylate superplasticizers cement interactions. Adjust dosages or switch to a compatible Polycarboxylate superplasticizers formulation if issues arise.
- Optimize mixing sequence: Add Polycarboxylate superplasticizers after initial water and aggregates to prevent premature adsorption onto cement particles.
- Use supplementary cementitious materials (SCMs): Incorporate fly ash, slag, or silica fume to modify cement reactivity and improve Polycarboxylate superplasticizers efficiency.
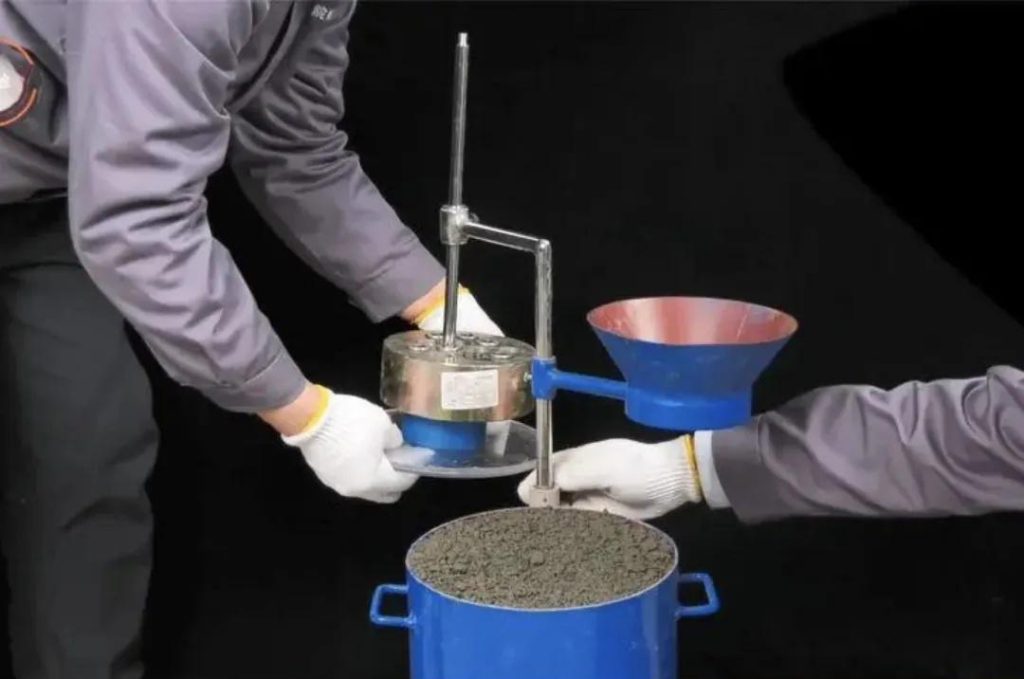
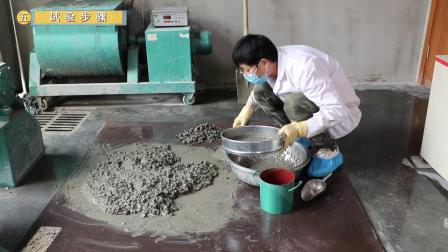
2. Excessive Slump Loss
Rapid slump loss reduces workability, making it difficult to place concrete. This is often linked to inadequate Polycarboxylate superplasticizers retention or chemical interactions.
Causes:
- High cement fineness: Finer cement particles absorb Polycarboxylate superplasticizers faster, accelerating slump loss.
- High ambient temperature: Elevated temperatures increase hydration rates, reducing Polycarboxylate superplasticizers effectiveness.
- Inadequate Polycarboxylate superplasticizers dosage: Low dosages may not provide sufficient steric hindrance to maintain fluidity.
Solutions:
- Adjust Polycarboxylate superplasticizers dosage: Increase the dosage slightly or switch to a high-range water reducer with better retention properties.
- Use retarding agents: Combine Polycarboxylate superplasticizers with retarders (e.g., gluconates) to slow hydration and extend workability.
- Cool concrete ingredients: Use chilled water or shaded aggregates to mitigate temperature effects.
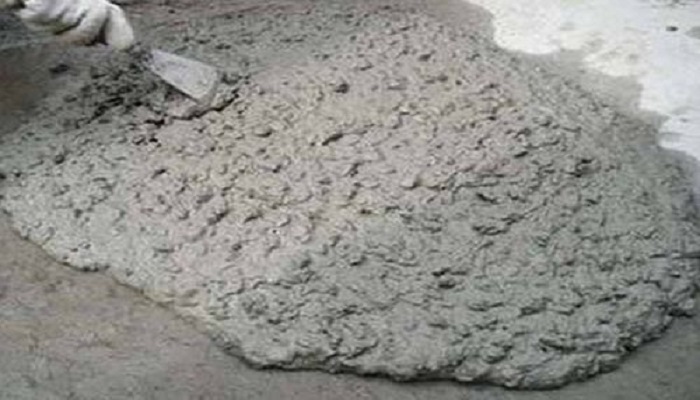
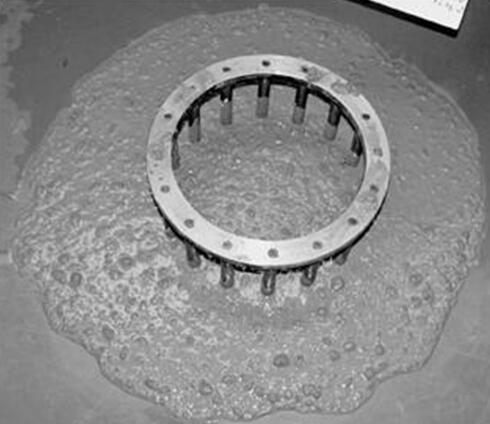
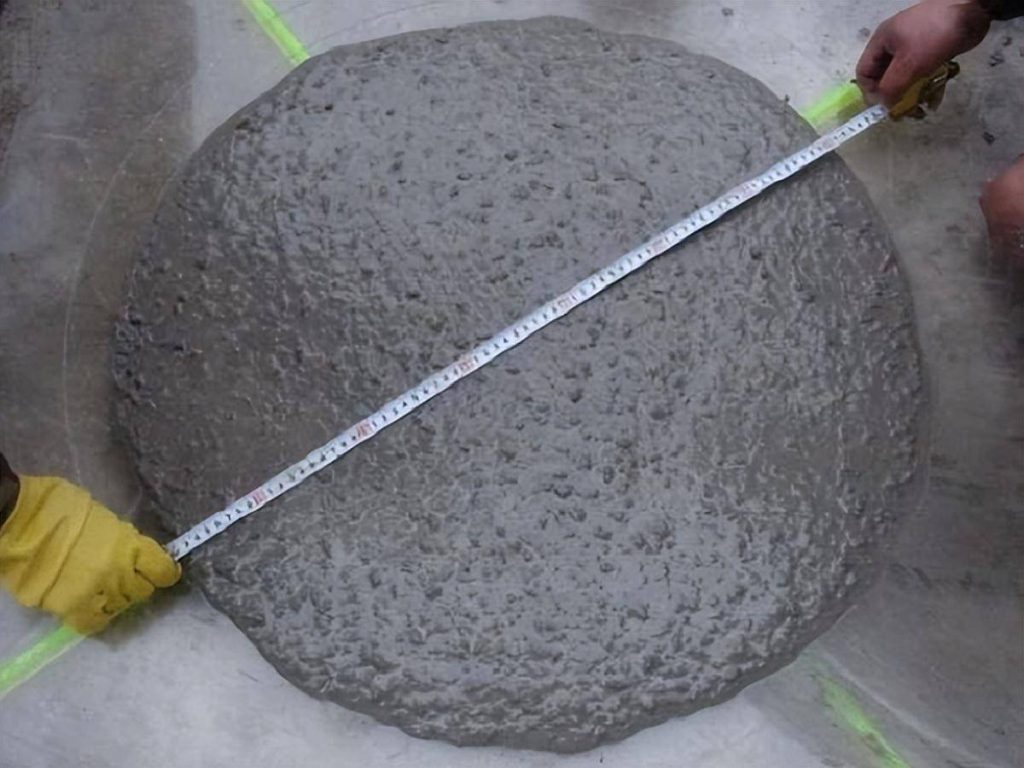
3. Delayed Setting or Reduced Strength
Excessive Polycarboxylate superplasticizers use or improper formulation can delay concrete setting or compromise compressive strength.
Causes:
- Overdosing Polycarboxylate superplasticizers: High dosages may retard hydration, leading to extended curing times.
- Incompatible admixtures: Combining Polycarboxylate superplasticizers with certain air-entraining agents or accelerators can disrupt setting behavior.
Solutions:
- Optimize dosage: Follow manufacturer recommendations and conduct trial mixes to determine the ideal Polycarboxylate superplasticizers concentration.
- Balance admixtures: Ensure compatibility between Polycarboxylate superplasticizers and other additives. Test combinations in advance.
- Adjust curing conditions: Provide adequate moisture and temperature control to promote proper hydration.
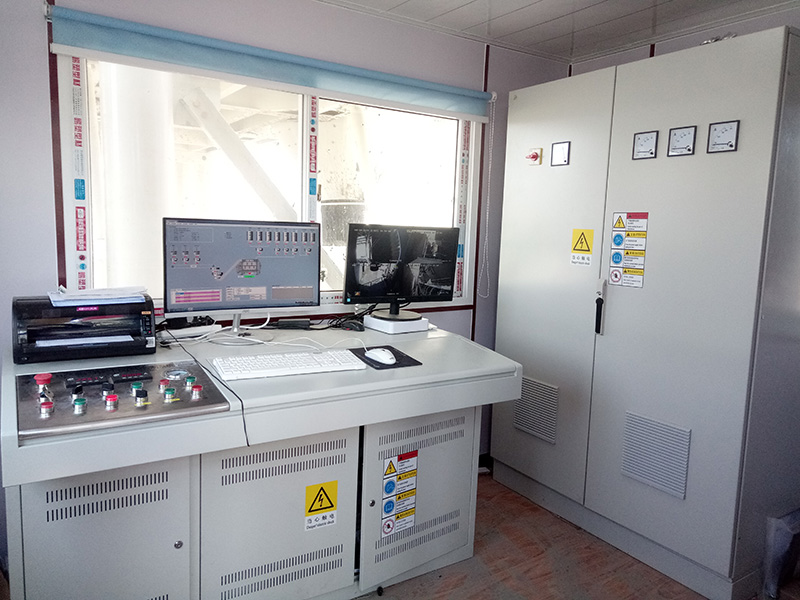
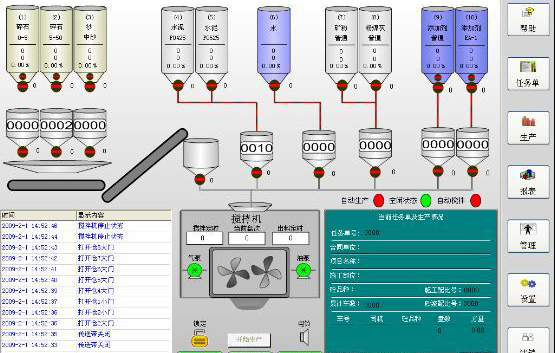
4. Air Entrainment Challenges
Polycarboxylate superplasticizers can sometimes stabilize excessive air bubbles, reducing concrete density and durability.
Causes:
- High Polycarboxylate superplasticizers dosage: Overuse can create unstable air voids.
- Impurities in aggregates: Clay or silt particles may adsorb Polycarboxylate superplasticizers, altering air-entrainment behavior.
Solutions:
- Use defoamers: Add silicon-based defoamers to control excessive air.
- Adjust aggregate grading: Ensure aggregates meet cleanliness standards to minimize Polycarboxylate superplasticizers adsorption.
- Monitor air content: Use ASTM C231 or pressure methods to maintain optimal air voids (3–6% for most concretes).
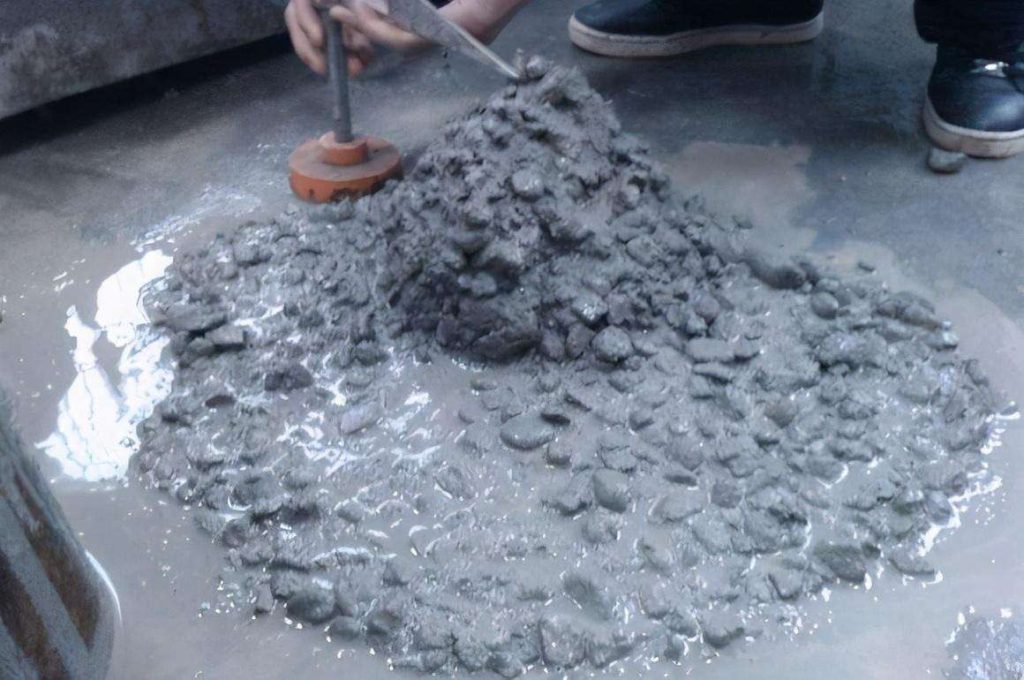
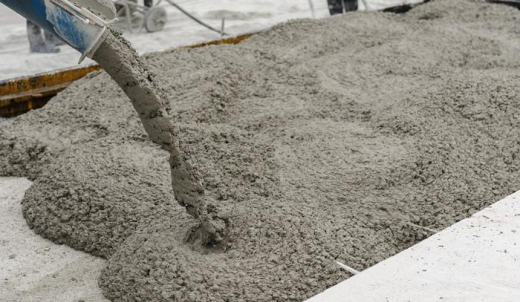
5. Segregation and Bleeding
Improper Polycarboxylate superplasticizers use can lead to segregation (particle separation) or bleeding (water migration to the surface).
Causes:
- Insufficient dosage: Low Polycarboxylate superplasticizers levels may fail to stabilize the mix, causing particles to settle.
- Excessive water reduction: Over-reducing water can increase viscosity and promote segregation.
Solutions:
- Optimize water-to-cement ratio (w/c): Maintain a balanced w/c ratio (typically 0.3–0.5) to ensure cohesive mixes.
- Add viscosity-modifying agents (VMAs): Incorporate cellulose ethers or synthetic polymers to enhance stability.
- Adjust mixing time: Ensure thorough blending to distribute Polycarboxylate superplasticizers evenly.
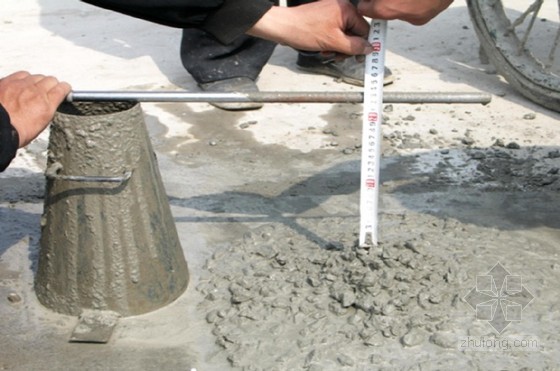
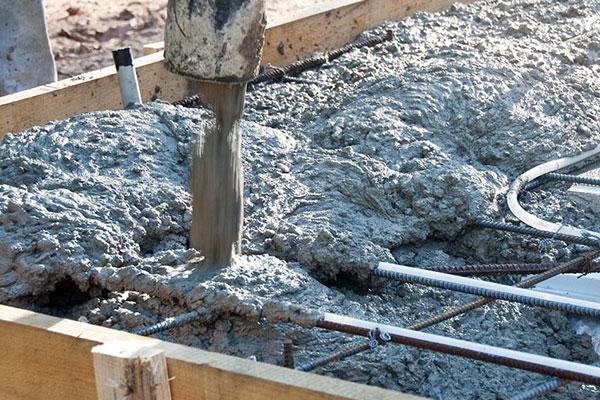
6. Cost Efficiency and Sustainability
While Polycarboxylate superplasticizers offer benefits, high costs or overuse can strain budgets. Additionally, improper disposal may harm the environment.
Solutions:
- Use hybrid systems: Combine Polycarboxylate superplasticizers with traditional naphthalene-based superplasticizers to reduce costs.
- Recycle wash water: Treat and reuse water from concrete mixing equipment to minimize waste.
- Adopt green Polycarboxylate superplasticizers: Choose bio-based or low-carbon Polycarboxylate superplasticizers formulations to align with sustainability goals.
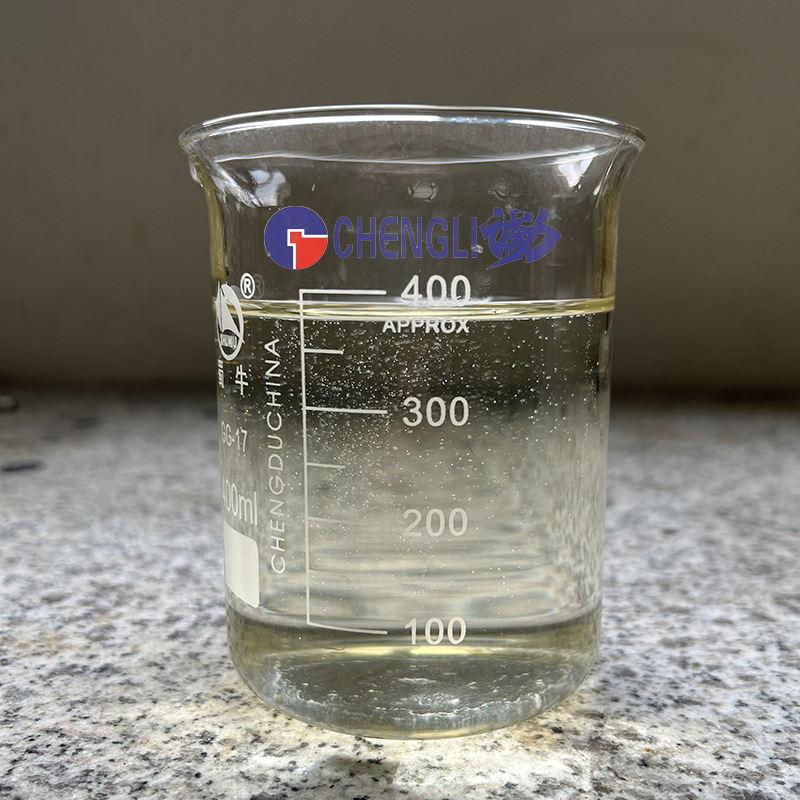
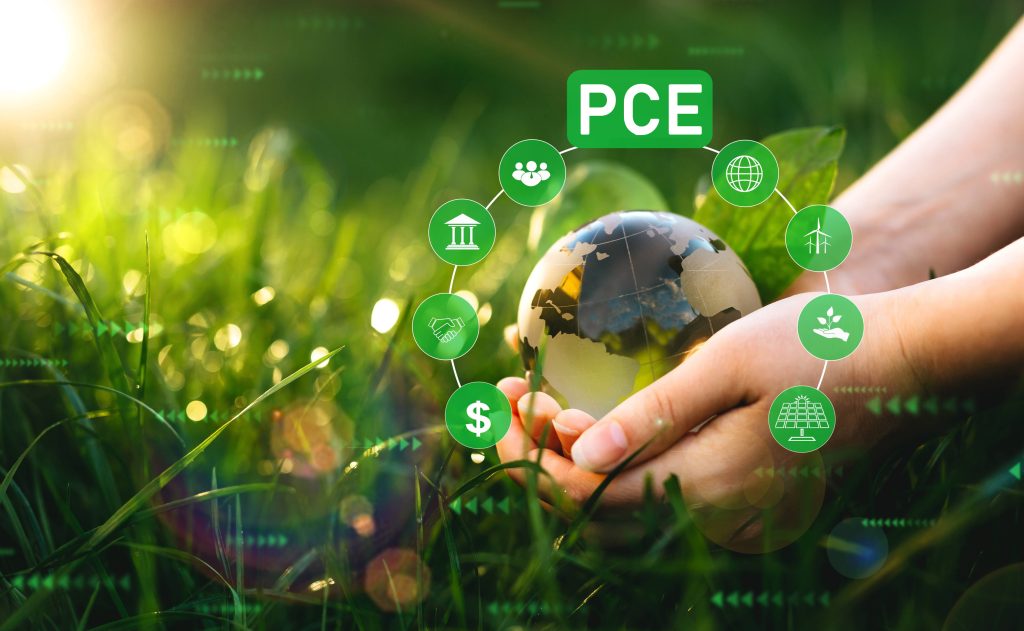
7. Case Studies and Best Practices
Case Study 1: High-Rise Construction in Dubai
A project using Polycarboxylate superplasticizers experienced severe slump loss in high temperatures. Solutions included:
- Switching to a Polycarboxylate superplasticizers with higher thermal stability.
- Adding a small amount of retarder to extend workability.
- Cooling aggregates with shade and chilled water.
Best Practices:
- Pre-test mixes: Always conduct trial batches before full-scale production.
- Monitor environmental conditions: Adjust Polycarboxylate superplasticizers dosages based on temperature, humidity, and sunlight exposure.
- Train staff: Ensure workers understand Polycarboxylate superplasticizers handling, mixing sequences, and troubleshooting protocols.
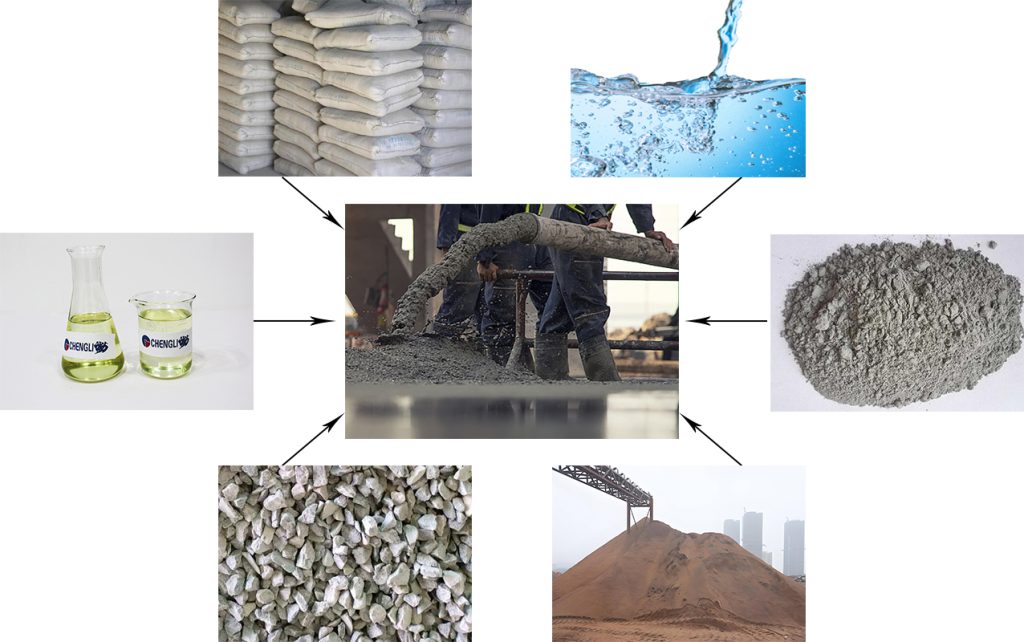
συμπέρασμα
Polycarboxylate superplasticizers are indispensable for modern concrete, but their effective use requires careful attention to compatibility, dosage, and environmental factors. By addressing common issues like slump loss, setting delays, and air entrainment, construction teams can achieve durable, cost-effective results. Regular testing, collaboration with suppliers, and adherence to best practices are key to maximizing Polycarboxylate superplasticizers performance. For complex challenges, consult with admixture experts or materials engineers to develop tailored solutions.