Maximizing the Dispersion Effect of الملدن المتفوق متعدد الكربوكسيلات in Cementitious Systems
1-Introduction
In the past few decades, polycarboxylate superplasticizers have attracted significant attention in the construction industry. Their unique properties, such as reducing the water demand in concrete or improving its workability with a relatively low dosage, make them an essential additive in modern concrete production. Polycarboxylate superplasticizers molecules possess a comb – like structure, consisting of a main chain with anionic groups (including carboxyl, sulfonic, and phosphate groups) and long grafted side chains (e.g., polyethylene glycol terminated with hydroxyl or methyl groups). The anionic groups on the main chain act as adsorption sites, interacting electrostatically with cement particles, while the side chains provide steric hindrance to prevent the flocculation of cement particles.
The adsorption of Polycarboxylate superplasticizers molecules on the surface of cement particles is a prerequisite for the dispersion of cement particles. Therefore, understanding and optimizing this adsorption process is crucial for maximizing the dispersion effect of Polycarboxylate superplasticizers in cementitious systems. Most previous studies have focused on the changes in the chain structure, especially the type and proportion of monomers, and their structure – activity relationships. However, there are still many aspects that need further exploration, such as the influence of Polycarboxylate superplasticizers conformation on the adsorption process.
2-The Influence of Polycarboxylate superplasticizers Molecular Structure on Dispersion
2.1 Monomer Type and Proportion
The type and proportion of monomers in Polycarboxylate superplasticizers play a fundamental role in determining its dispersion performance. For instance, the ratio of carboxylic groups to polyethylene glycol (PEG) monomethyl ether (AER) can significantly affect the dispersing ability of Polycarboxylate superplasticizers. When the AER is within a certain range, different monomer compositions result in different dispersion capabilities. As research has shown, for Polycarboxylate superplasticizers with side – chain lengths, Polycarboxylate superplasticizers with a lower methyl content in the main chain exhibits better initial dispersion performance. For example, in systems where AER ≤ 3.5, the order of dispersion ability from high to low is: Polycarboxylate superplasticizers with a medium methyl content in the main chain > Polycarboxylate superplasticizers with a low methyl content in the main chain > Polycarboxylate superplasticizers with a high methyl content in the main chain. And for AER ≤ 7.0, the dispersion ability increases as the methyl content in the main chain decreases.
2.2 Chain Flexibility and Hydrophilicity
Chain flexibility and hydrophilicity are also important factors. The flexibility of the main chain affects the way Polycarboxylate superplasticizers molecules interact with cement particles. A more flexible chain may be able to adjust its conformation more easily to achieve better adsorption on the complex surface of cement particles. Hydrophilicity, on the other hand, influences the solubility of Polycarboxylate superplasticizers in the aqueous phase of the cementitious system. If the Polycarboxylate superplasticizers is not sufficiently hydrophilic, it may not be able to disperse evenly in the water, reducing its effectiveness in dispersing cement particles. By adjusting the chemical structure of the main chain, such as changing the content of certain groups like methyl groups, the flexibility and hydrophilicity of the Polycarboxylate superplasticizers can be modified.
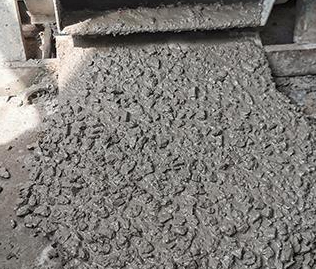
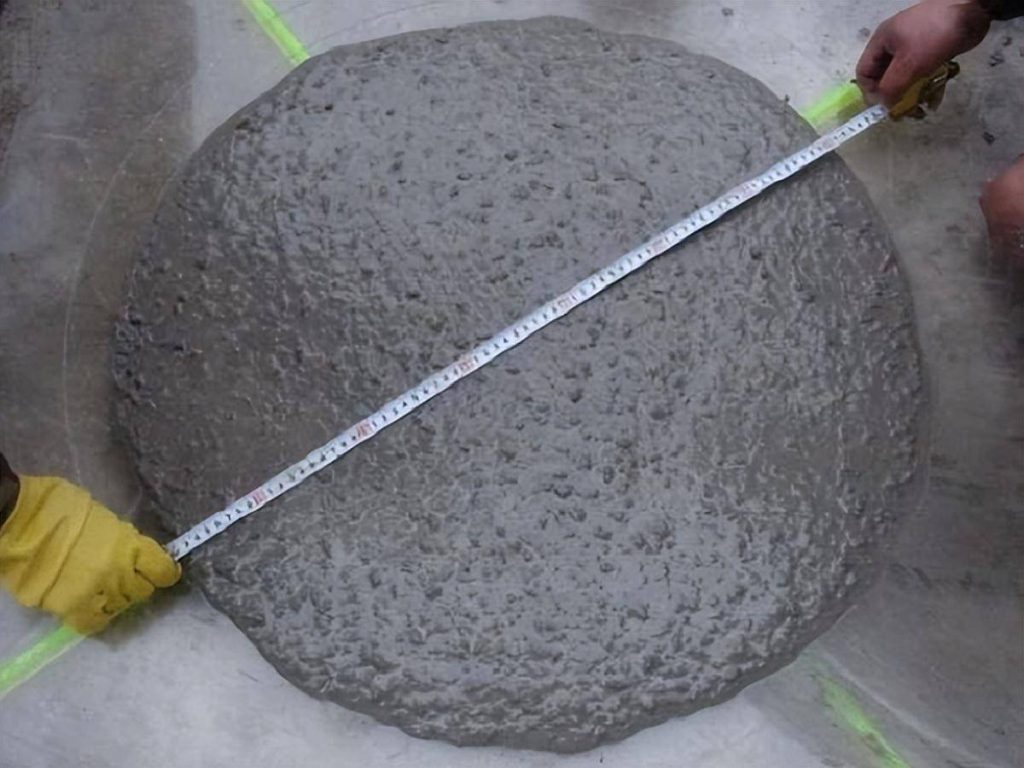
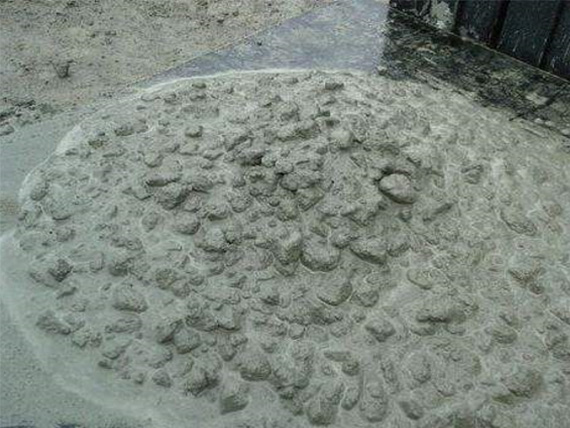
3-Interaction between Polycarboxylate superplasticizers and Cement Particles
3.1 Adsorption Mechanism
The adsorption of Polycarboxylate superplasticizers on cement particles is mainly through electrostatic interaction between the anionic groups on the Polycarboxylate superplasticizers main chain and the positively charged sites on the surface of cement particles. Once adsorbed, the Polycarboxylate superplasticizers molecules form a layer around the cement particles. The thickness and stability of this adsorbed layer are crucial for the dispersion effect. A thicker and more stable adsorbed layer can provide better steric hindrance, preventing the agglomeration of cement particles. However, the presence of various ions in the cementitious system, such as calcium ions, can compete with the Polycarboxylate superplasticizers for adsorption sites on the cement particles, affecting the adsorption amount and conformation of Polycarboxylate superplasticizers.
3.2 Influence of Cement Composition
The chemical composition and mineralogy of cement also have a significant impact on the interaction with Polycarboxylate superplasticizers. Different types of cement, with varying contents of tricalcium silicate (C3S), dicalcium silicate (C2S), tricalcium aluminate (C3A), and tetracalcium aluminoferrite (C4AF), will interact differently with Polycarboxylate superplasticizers. For example, C3A – rich cements tend to have a higher water demand and a stronger adsorption capacity for Polycarboxylate superplasticizers. This can lead to a higher dosage requirement of Polycarboxylate superplasticizers to achieve the desired dispersion effect. In addition, the fineness of cement particles also affects the specific surface area available for Polycarboxylate superplasticizers adsorption. Finer cement particles have a larger specific surface area, which may require more Polycarboxylate superplasticizers to cover the surface and achieve effective dispersion.
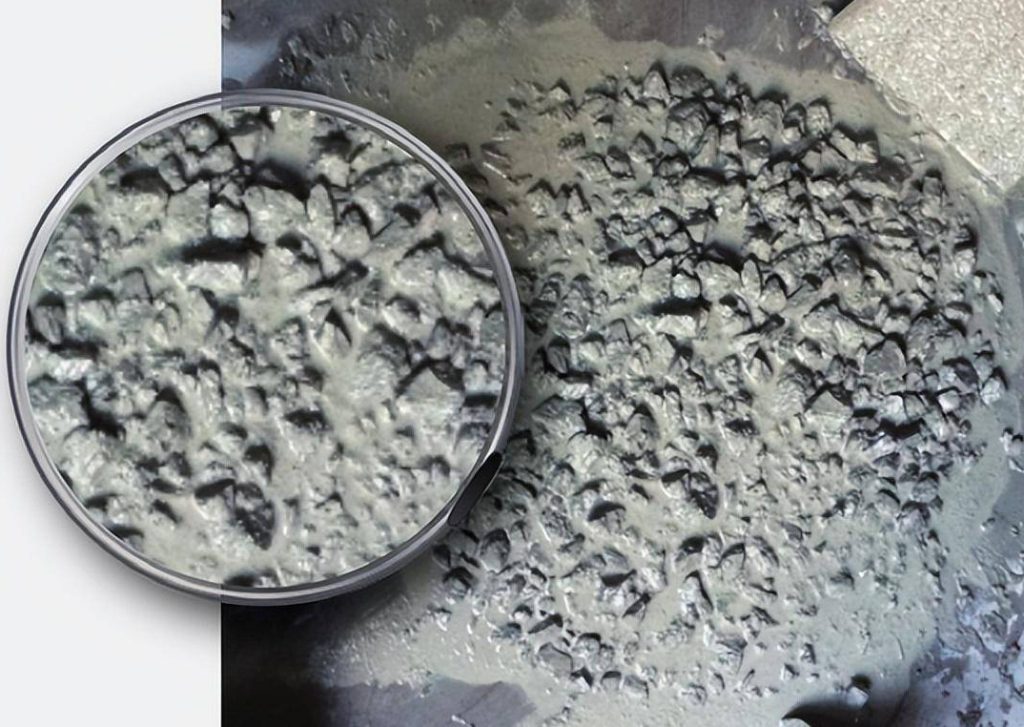
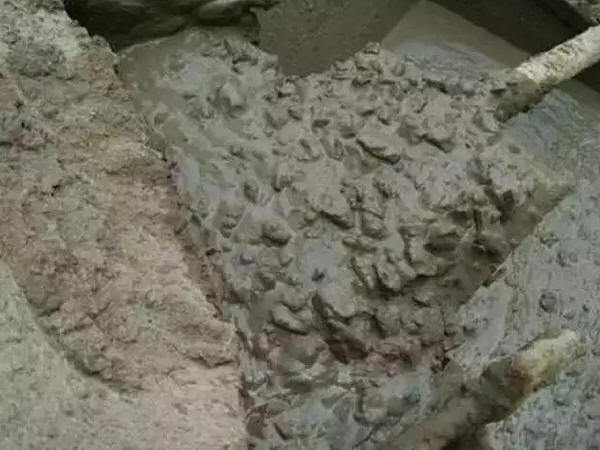
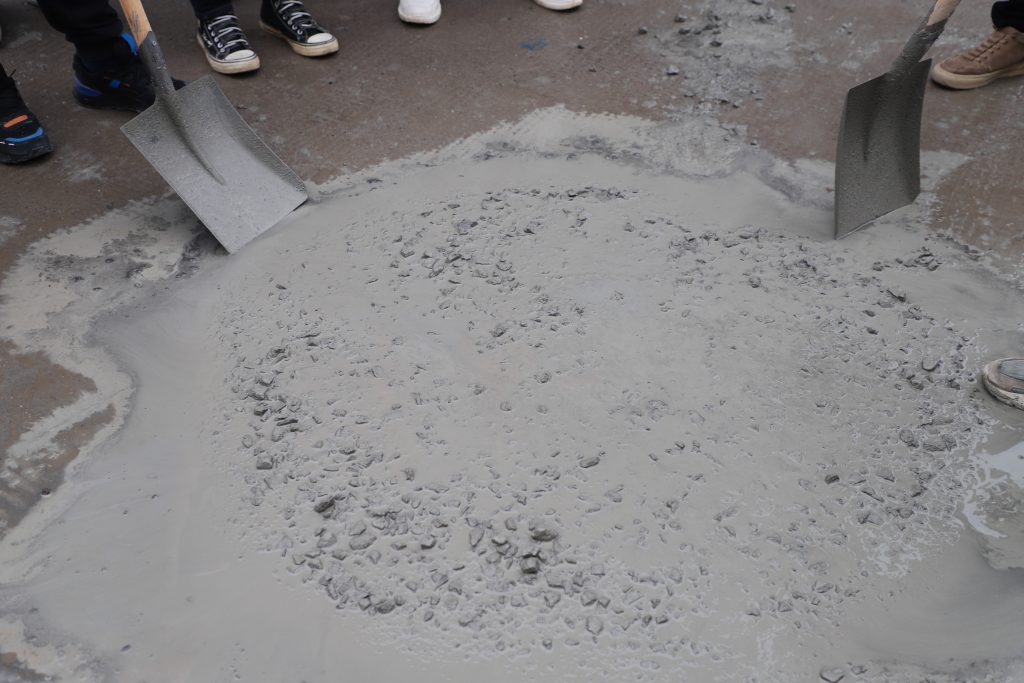
4-Optimization Methods for Maximizing Dispersion
4.1 Molecular Design and Modification
Based on the understanding of the influence of Polycarboxylate superplasticizers molecular structure on dispersion, targeted molecular design and modification can be carried out. For example, by precisely controlling the ratio of different monomers during the synthesis of Polycarboxylate superplasticizers, the optimal chain structure can be obtained. In addition, introducing specific functional groups to adjust the flexibility and hydrophilicity of the chain can also improve the dispersion performance. For instance, increasing the length of the side chains appropriately can enhance the steric hindrance effect, but it should be noted that an overly long side chain may also lead to entanglement and reduced mobility of the Polycarboxylate superplasticizers molecule.
4.2 Selection of Compatible Cement and Polycarboxylate superplasticizers
When using Polycarboxylate superplasticizers in a cementitious system, it is necessary to select a compatible combination of cement and Polycarboxylate superplasticizers. This requires considering the chemical composition, fineness, and other properties of the cement. For example, for cements with a high C3A content, Polycarboxylate superplasticizers with a relatively high adsorption capacity and good dispersion stability should be selected. At the same time, it may be necessary to conduct pre – tests to determine the optimal dosage of Polycarboxylate superplasticizers for different cements to achieve the best dispersion effect while minimizing the cost.
4.3 Control of the Mixing Process
The mixing process also has a great impact on the dispersion effect of Polycarboxylate superplasticizers. Appropriate mixing speed and time can ensure that Polycarboxylate superplasticizers is evenly distributed in the cementitious system and fully interacts with cement particles. For example, in the initial stage of mixing, a relatively slow mixing speed can be used to allow Polycarboxylate superplasticizers to gradually adsorb on the surface of cement particles. Then, as the mixing progresses, an appropriate increase in the mixing speed can help to break up possible agglomerates and further disperse the cement particles. In addition, the order of adding materials, such as whether to add Polycarboxylate superplasticizers first or mix it with water first, can also affect the final dispersion effect.
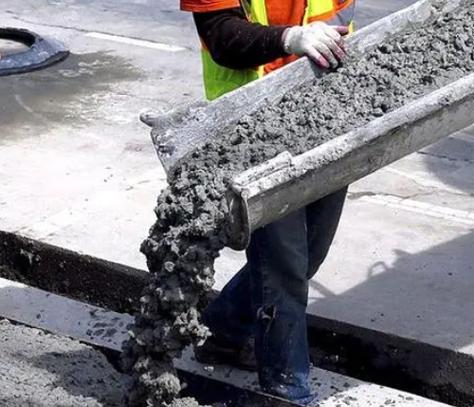
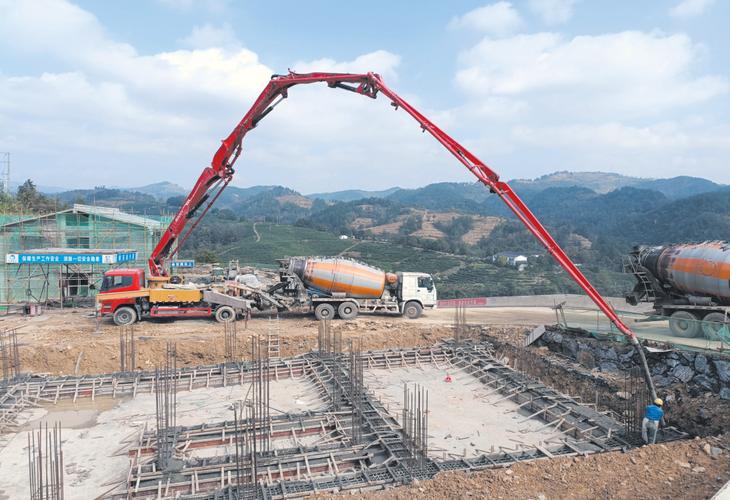
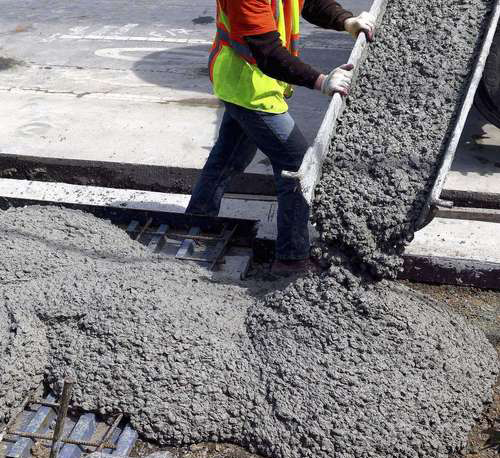
5-Measuring the Dispersion Effect
5.1 Flowability Test
One of the most common methods to measure the dispersion effect of Polycarboxylate superplasticizers in a cementitious system is the flowability test. In this test, a certain amount of cement, water, and Polycarboxylate superplasticizers are mixed according to a specific ratio. Then, the mixture is placed in a standardized mold (such as a conical mold), and the mold is quickly removed. The diameter of the spread of the cement paste is measured, and a larger spread diameter indicates better flowability and stronger dispersion ability of Polycarboxylate superplasticizers.
5.2 Rheological Measurement
Rheological measurement can also provide in – depth information about the dispersion state of the cementitious system. By measuring the viscosity and yield stress of the cement paste under different shear rates, we can understand the internal structure and the degree of dispersion of the cement particles. A lower viscosity and yield stress at a given shear rate suggest that the Polycarboxylate superplasticizers has effectively dispersed the cement particles and reduced the internal friction within the system.
5.3 Adsorption Measurement
Measuring the amount of Polycarboxylate superplasticizers adsorbed on cement particles is also important. This can be done using methods such as total organic carbon (TOC) analysis. By comparing the concentration of Polycarboxylate superplasticizers in the solution before and after mixing with cement, the amount of Polycarboxylate superplasticizers adsorbed by the cement particles can be calculated. Understanding the adsorption amount can help us adjust the dosage of Polycarboxylate superplasticizers and optimize the dispersion process.
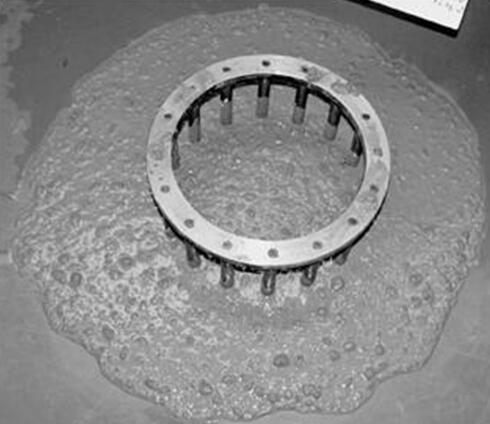

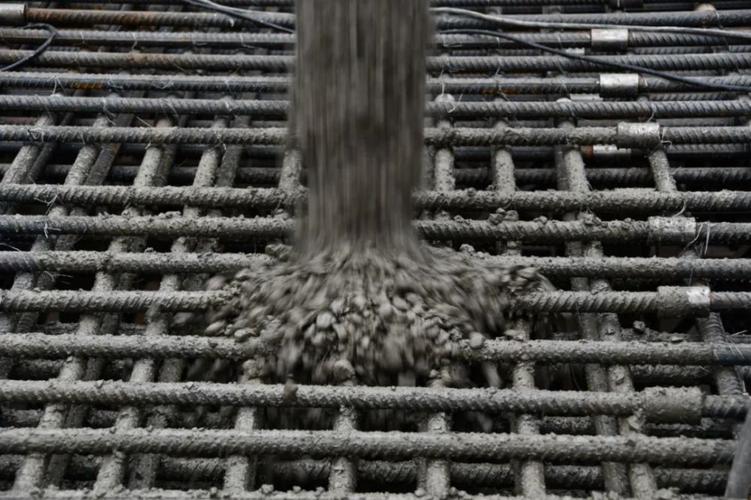
6-Conclusion
Maximizing the dispersion effect of polycarboxylate superplasticizer in cementitious systems requires a comprehensive consideration of multiple factors, including the molecular structure of Polycarboxylate superplasticizers, its interaction with cement particles, the selection of compatible materials, and the control of the mixing process. Through in – depth research on these aspects and continuous optimization of the relevant parameters, we can improve the performance of Polycarboxylate superplasticizers in cementitious systems, reduce the water demand in concrete, and improve the workability and durability of concrete. This not only promotes the development of the concrete industry but also has important economic and environmental significance. Future research can focus on further exploring the detailed mechanisms of Polycarboxylate superplasticizers – cement interaction at the molecular level and developing more efficient and environmentally friendly Polycarboxylate superplasticizers products.
يتوفر فريقنا الفني المحترف على مدار الساعة طوال أيام الأسبوع لمعالجة أي مشكلات قد تواجهها أثناء استخدام منتجاتنا. ونحن نتطلع إلى تعاونكم!