In high-temperature environments (30℃+), concrete placement faces critical challenges due to accelerated cement hydration, leading to rapid slump loss and reduced workability. Maintaining slump retention for at least 4 hours is essential for complex pours, such as large-scale foundations or precast elements, where prolonged handling and placement are required. This article explores how advanced polycarboxylate superplasticizer (PCE) and solid concrete water reducing agent formulations, supported by innovative concrete admixtures manufacturers, address slump retention in extreme heat while ensuring structural integrity.
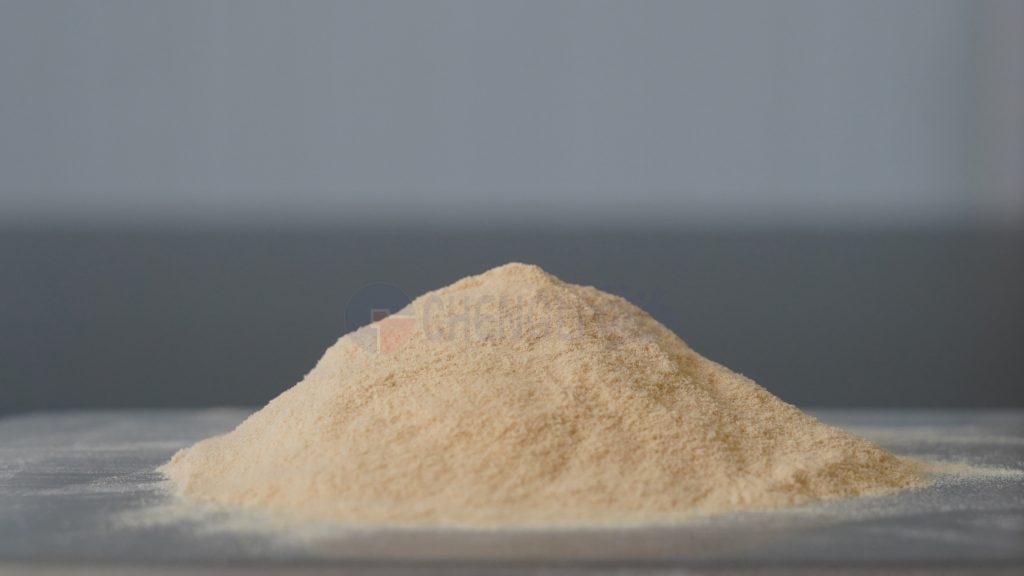
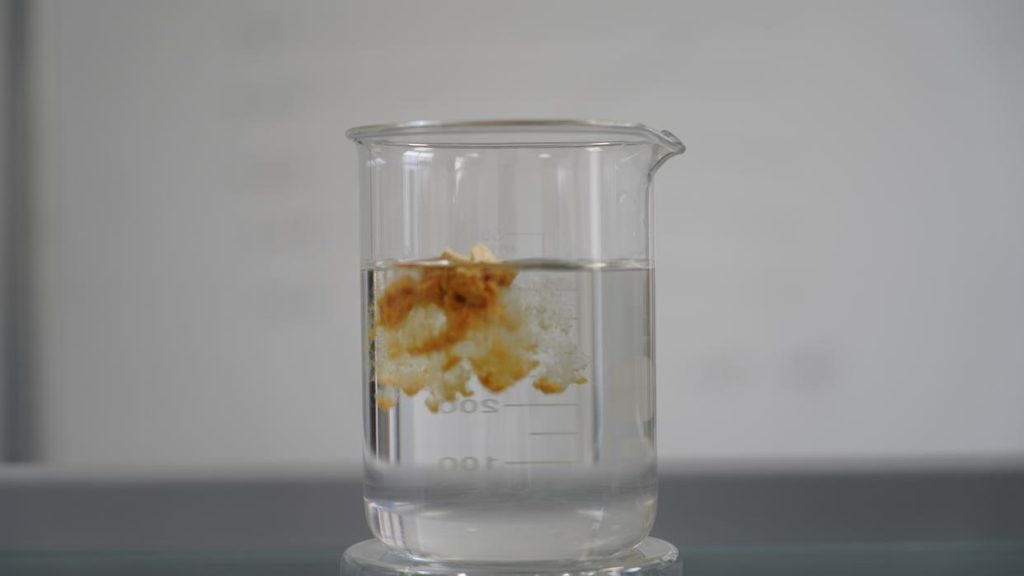
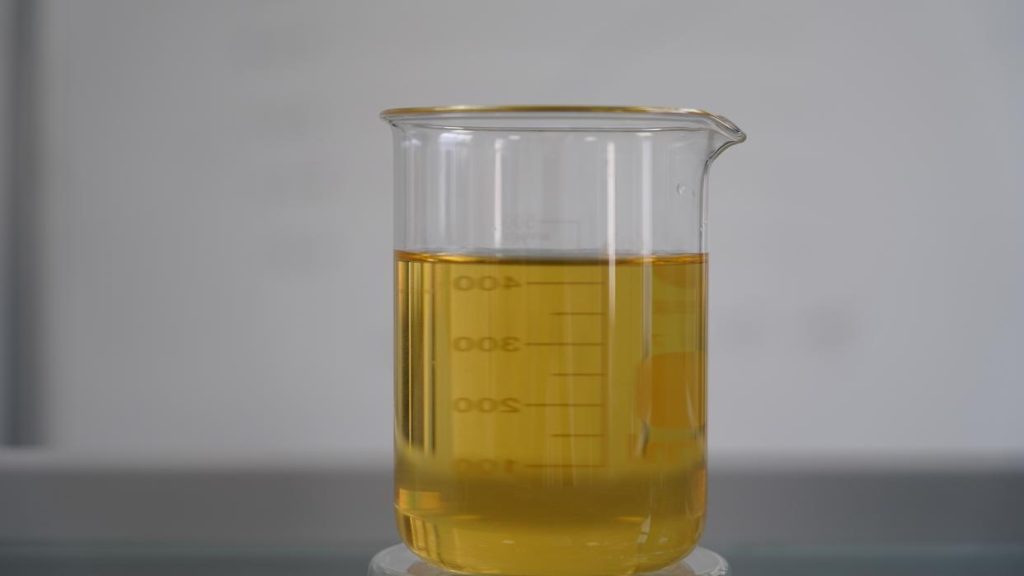
The Impact of High Temperature on Concrete Workability
At 30℃, cement hydration rates increase by 30-40% compared to standard conditions, causing:
- Rapid flocculation: Cement particles aggregate faster, reducing paste fluidity.
- Shortened setting time: Initial set can occur within 2-3 hours, compromising placement efficiency.
- Increased plastic shrinkage: Higher evaporation rates lead to cracking risks.
Traditional water reducers struggle to maintain slump beyond 90 minutes in such conditions. However, modern concrete water reducing agents like polycarboxylate superplasticizers offer superior dispersion and retardation capabilities.

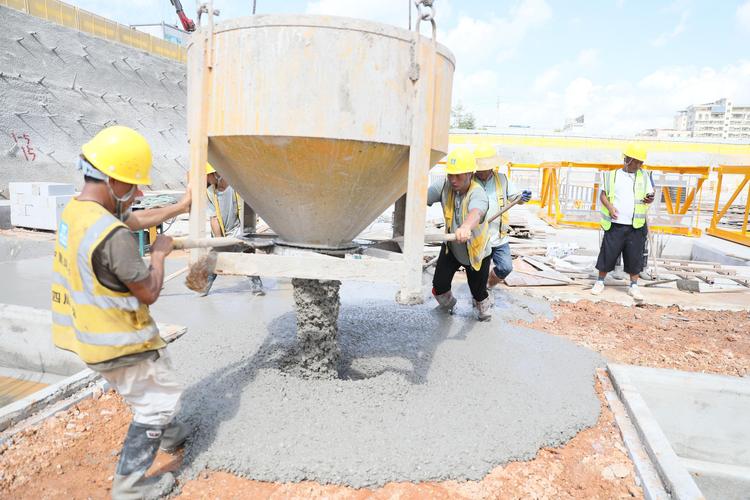
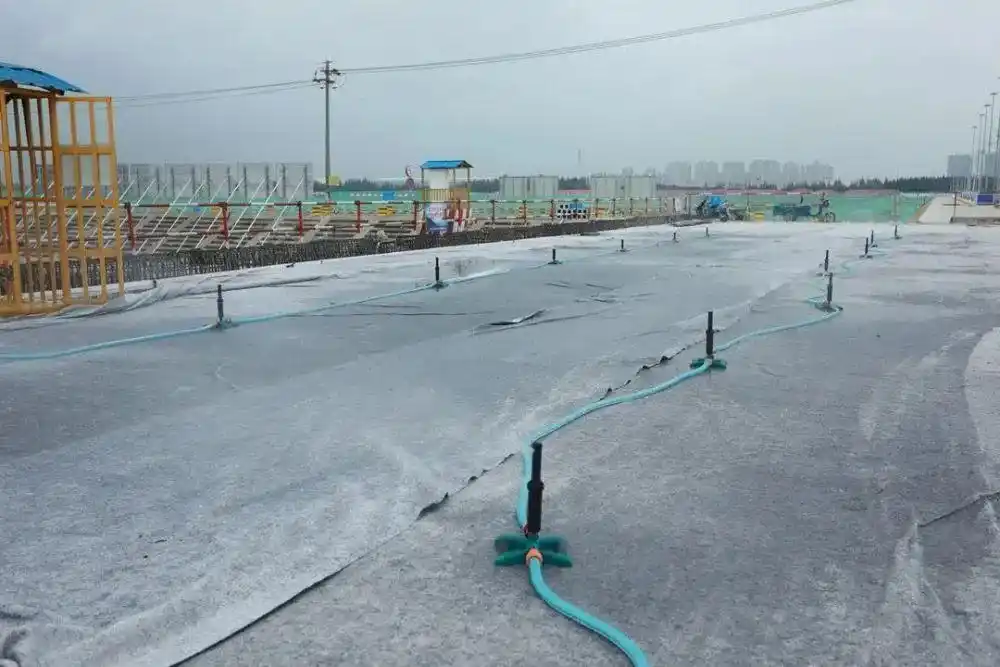
Technical Solutions for Slump Retention
1. Polycarboxylate Superplasticizer (PCE) Technology
PCEs feature a comb-like molecular structure that:
- Enhances steric hindrance: Disperses cement particles effectively, delaying flocculation.
- Modulates hydration kinetics: Incorporates retarder groups (e.g., hydroxyl carboxylic acids) to slow calcium silicate hydration.
- Sustains workability: Achieves 4-hour slump retention with dosages as low as 0.8-1.2% by cement weight.
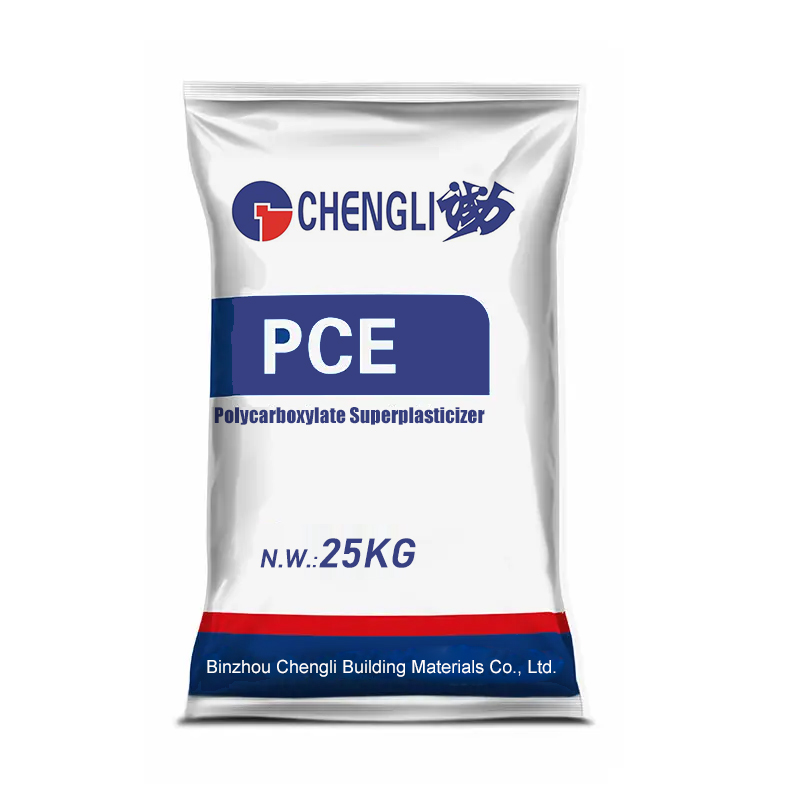
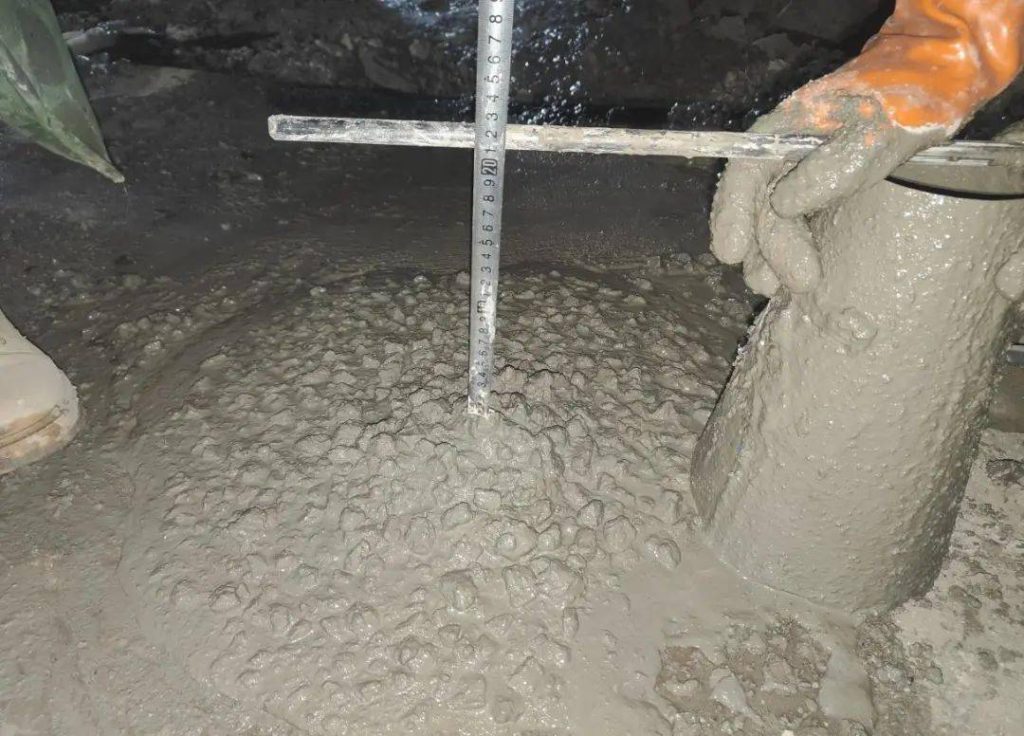
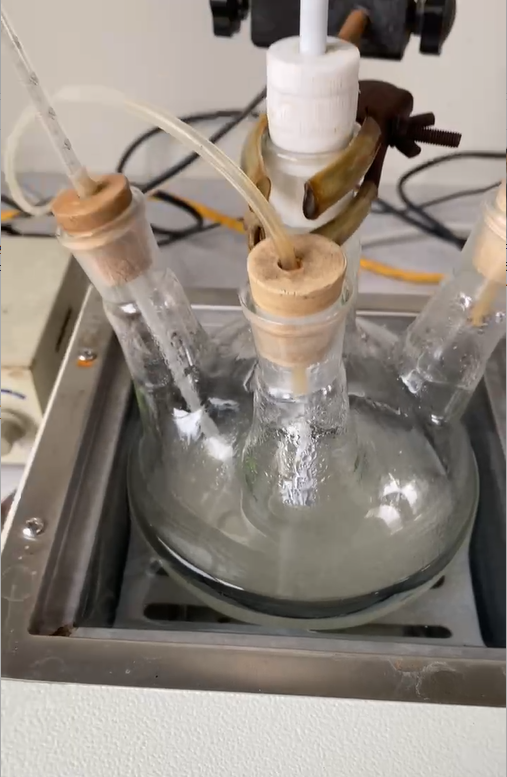
2. Solid Concrete Water Reducing Agent Advantages
Solid formulations (e.g., powder or granular PCEs) offer:
- Stability in high humidity: Reduced risk of microbial growth compared to liquid admixtures.
- Precision dosing: Easier integration into automated batching systems for large projects.
- Cost efficiency: Lower transportation costs due to reduced water content in the product.
A leading concrete admixtures manufacturer recently developed a hybrid system combining PCE with a solid retarder, achieving 200mm slump retention at 4 hours in 30℃ tests.
Case Study: High-Temperature Concrete Mix Design
Mix Parameters
Component | Content (kg/m³) | Role |
---|---|---|
Portland Cement | 450 | Binder |
Coarse Aggregate | 1100 | Structural skeleton |
Fine Aggregate | 700 | Filler |
Water | 145 | Hydration (w/c = 0.32) |
PCE Superplasticizer | 5.4 (1.2% by cement) | Slump retention & water reduction |
Solid Retarder | 0.9 (0.2% by cement) | Hydration control |
Test Results
- Slump Retention: 210mm at 0h → 195mm at 4h (30℃ curing).
- Compressive Strength: 35MPa at 7 days (meet design requirements).
- Thermal Analysis: Peak hydration temperature reduced by 15℃ vs. conventional mixes.
Key Considerations for Admixture Selection
- Compatibility: Ensure PCE-retarder systems align with local cement chemistries (e.g., C3A content).
- Dosing Precision: Automated systems minimize errors in high-temperature batching.
- Sustainability: Look for low-VOC, bio-based retarders to meet green building standards.
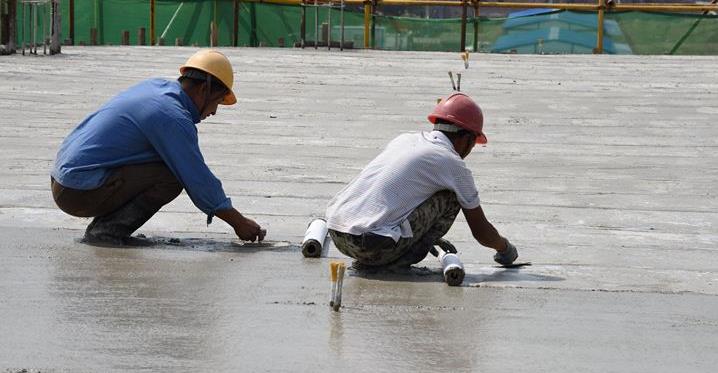
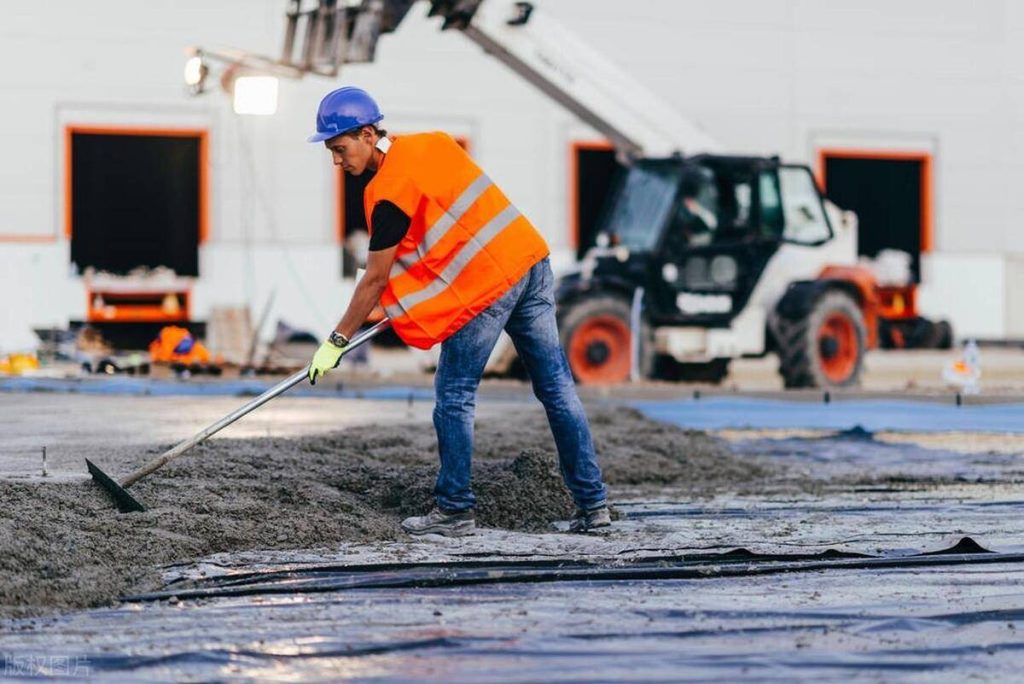
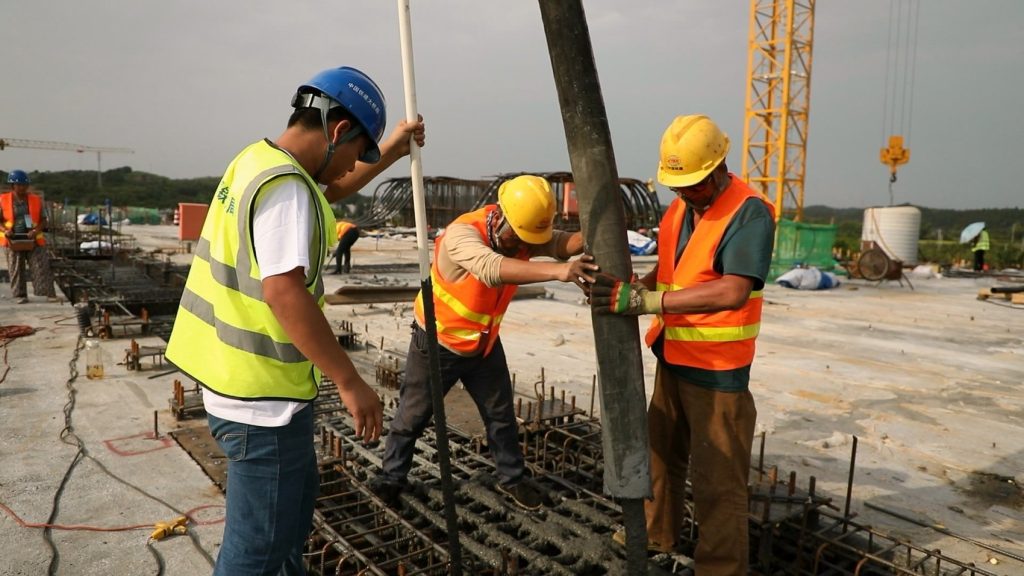
Conclusion
In 30℃ environments, achieving 4-hour slump retention requires a strategic combination of polycarboxylate superplasticizer and solid concrete water reducing agent technologies, supported by expertise from concrete admixtures manufacturers. These solutions not only address workability challenges but also enhance long-term durability by optimizing hydration kinetics. As climate change drives more extreme weather conditions, advanced admixtures will remain critical for maintaining concrete performance in high-temperature applications.
For Tailored Advice Or Technical Support, Contact Our Team At Cl18366819567@Gmail.Com.